共计 3563 个字符,预计需要花费 9 分钟才能阅读完成。
统计过程控制(SPC)是一种借助数理统计方法的过程控制工具,广泛应用于制造业和服务业中,以保证产品或服务质量,提高生产效率。我来介绍一下SPC的基础知识,包括其生命特征、关系链、控制原理,并进一步探讨控制图和过程能力分析的具体应用。
SPC的基础知识
SPC之父:休哈特
SPC的起源可以追溯到20世纪20年代,被誉为“SPC之父”的沃尔特·休哈特(Walter A. Shewhart)首次提出了统计质量控制理论。休哈特认为,制造过程中的变异可以分为两种:特殊原因(也称为偶然原因)和普通原因(也称为系统原因)。他提出了通过控制图来区分这两种变异的方法,为SPC的发展奠定了基础。
SPC的定义和目的
SPC是一种应用统计分析技术对生产过程进行监控,科学的区分出生产过程中产品质量的随机波动与异常波动,从而对生产过程的异常趋势提出预警,以便生产管理人员及时采取措施,消除异常,恢复过程的稳定,从而达到提高和控制质量的目的。SPC不仅关注产品的最终质量,还关注生产过程的稳定性和可控性,通过预防和控制质量问题的发生,提高生产效率和客户满意度。
SPC管理的特点
SPC管理的特点可以总结为以下几点:
-
全员参与:SPC要求全员参与质量控制活动,不仅限于质量控制部门。每个员工都应该对质量负责,积极参与质量改进活动。 -
预防为主:SPC强调事先控制,通过监控生产过程的变化,及时发现潜在问题并采取措施进行预防,避免质量问题的发生。 -
用数据说话:SPC依靠数据来分析和判断生产过程的稳定性。通过收集和分析生产数据,可以客观地评估生产过程的性能和质量水平。
产品检验与SPC的链
传统的产品检验是在生产结束后对产品进行检验,只能剔除不合格品,无法预防不合格品的产生。而SPC则强调在生产过程中进行监控,通过数据分析提前发现潜在问题,从而防止不合格品的产生。SPC与产品检验相辅相成,共同构成了一个完整的质量控制体系。
SPC的组成链
SPC的核心组成包括平均值、极差、标准差(σ)、中位数、单值等统计量。这些统计量用于描述和监控生产过程的变化,帮助识别异常波动。通过计算和分析这些统计量,可以对生产过程的稳定性和可控性进行客观评估。
SPC的工具链
SPC的工具链主要包括各种QC工具,如控制图、直方图、帕累托图、因果图等。这些工具在SPC中起着至关重要的作用。控制图用于监控生产过程的变化,及时发现潜在问题;直方图用于展示数据的分布情况,帮助识别异常数据;帕累托图用于分析质量问题的主要原因,为质量改进提供依据;因果图用于分析质量问题与各种因素之间的因果关系,为制定改进措施提供支持。
SPC应用
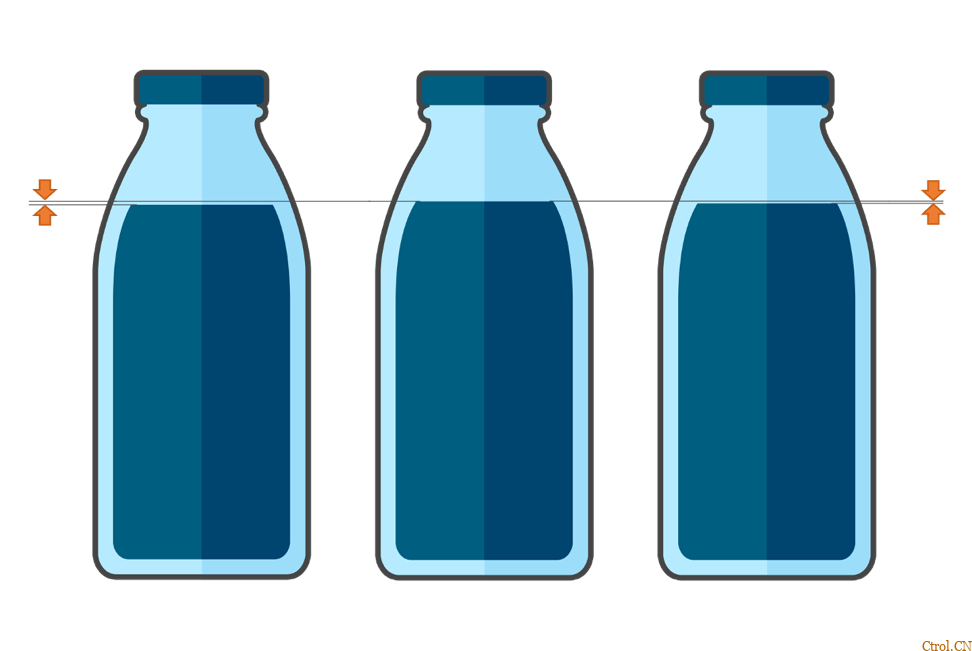
这里我们要引入一个概念-“变差”,变差不是指变得更差的意思,而是“在一定范围内波动带来的偏差”,就像世界上没有完全相同的两片树叶一样,工厂生产的产品之间都会存在变差。比如,同一批螺栓的长度,一批铸件的重量,饮料灌装的高度都会有些不同,这种变化就是变差。
就如刚才所说,即使再先进的工艺,也不能保证两瓶饮料的灌装是完全相同的,总会有些细微的差别。
这种细微的差别和我们的工艺方法、工艺能力、材料特性等一些固有因素有关。虽然会产生一些波动,但这种波动是在一个固定范围内的。比如我们常说的公差范围。
这种变差是固有的、普遍的、稳定的,并且发生在一个可控和可接受的的范围内,引起这种原因的变差就叫做“一般原因”。
但是某天你买到了一瓶只装了一半的饮料,或者在快餐店买到了你一份没有加生菜的汉堡,这很有可能是因为设备的故障或者员工的操作失误造成的。
那么这时产生的变差就不再是一种固有和普遍的波动,而是由于一些特殊的变化造成的。
因为这种变化是随机的,不可预期的(比如我们不太会预测到员工什么时候会操作失误),这种变化我们称之为特殊原因。
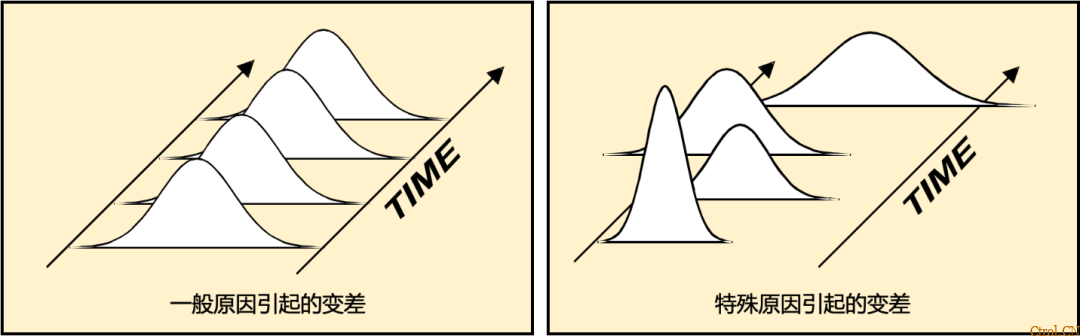
如果一个过程的变差都是由一般原因引起的,那么我们就说这个过程处于稳定的统计受控状态;如果一个过程的变差中不仅包含了一般原因,还包含了特殊原因,我们就说这个过程处于统计不受控的状态。
前面我们提到过,一般原因导致的变差是固有的、普遍的、稳定的,那就意味着这些变差也始终持续保持在一个稳定状态,那么未来我们的质量表现就是可以预期的。
而如果一个过程是不稳定不受控的状态,就意味着出现质量问题的可能性完全无法预测,质量表现忽高忽低,某段时间可能非常优秀,而另一段时间可能非常糟糕。
从前面我们知道,了解一个过程是否处于稳定受控的状态非常重要,那么我们就需要有一种方法能够简单的判断和描述一个过程是否稳定受控,这个工具就是SPC。
SPC是一种基于中心极限定理来绘制图表的形式来监控一个过程。用来实现下面的目的:
SPC是随时间变化来统计数据的图表,标中的每一个点都代表收集到的一个或一组数据,并将它们连线来表现出数据随时间的变化趋势。
与普通的折线图不同的是,SPC上会有三条线,分别是数据的上控制限,下控制限和均值线。这些线和数据点的组合帮我们来判断一个过程是不是稳定受控。
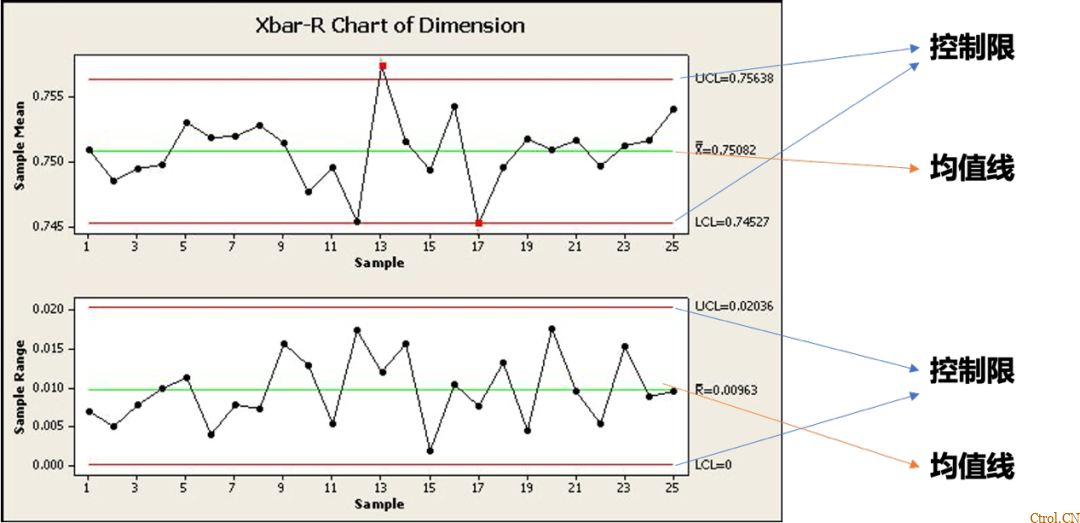
控制限:是根据收集到的数据计算出来的两条虚拟线,它表示如果一组数据处于稳定受控的状态,那么这组数据的边界应该在哪里。
均值线:数据或数据组的平均值。
一般来说,一个稳定受控的过程,它的数据产生的图形形状应该是随机的,并且所有的点都应在控制限内。如果上控制下限之间被分成三分的话, 那么2/3的点都应落在中心线周围1/3的区域内。
符合下面几种情况的SPC会被判定为不稳定不受控的状态:
a) 超出控制限
超出控制限的点就是个别的高点或低点。
b) 点贴近控制限
如果控制图上的点不能满足2/3的点落在中心线周围1/3区域内,那么就有很多点贴近控制限。
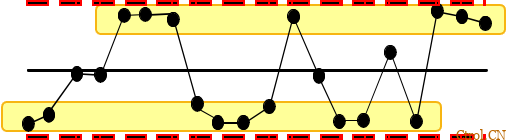
c) 点贴近中心线
如果几乎所有的点都落在均值线周围1/3区域内,那么这些点就是贴近均值线。
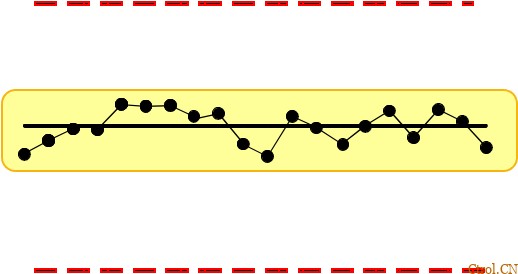
d) 在水平上突然转变
7个以上的点连续地上升或下降或者是这些点由均值线的一侧移动到另一侧。
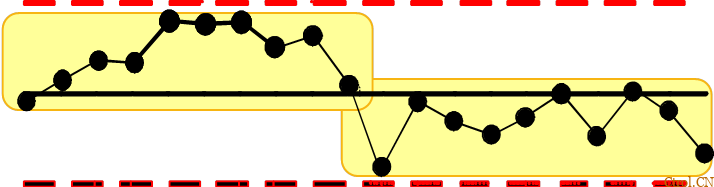
e) 出现明显趋势
出现明显的上升或者下降的趋势,就好像随着时间的变化,数据在同步的上升或下降。
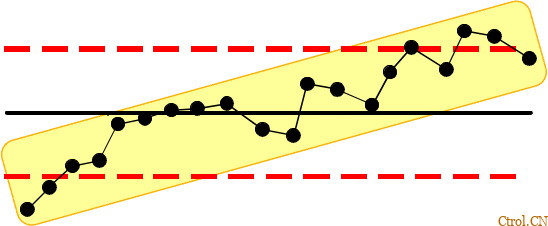
f) 周期性
连续上升和连续下降的点构成一个周期,好象这些点依靠时间有规律的变化。
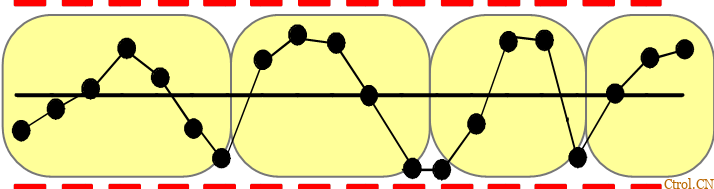
这里要说明一点,不稳定不受控的过程肯定是一个不好的质量过程,需要我们针对特殊原因去进行控制和解决。比如员工操作的防错和标准化,设备运行的稳定性等等。
但是稳定受控的过程并不一定是一个好的质量过程,因为稳定受控只能说明目前的过程是可控的,但能力未必达到客户的要求。
还拿饮料的例子来说,如果两瓶饮料高度的差异稳定在1mm,客户是能够接受的;如果稳定波动在1cm,虽然也是一种稳定,但客户就不会接受这样的产品,这就需要我们从工艺和制程上来降低这种稳定的波动,也就是常说的“过程能力”的提升。
知道了什么是SPC,那我们就要知道什么情况下,如何去做SPC。实际上SPC是可以应用在所有的管理流程上的,但为了更高效的使用SPC,我们建议大家从下面几个方向来思考:
所以怎么做SPC的问题,可以具体细化成如下几点:
1、确定哪些关键属性要做SPC?
一般来说,所有对最终质量有影响的过程控制点,都需要进行SPC统计,比如某个零件尺寸、重量等等。
2、确定数据收集的频次?
这是一个持续的过程,如果无法持续收集数据,就先努力将生产稳定下来。数据收集通常是固定频次的,比如:
每小时一次
上下午各一次
每班统计一次等等
3、数据取样的数量是多少?
根据实际的情况需要,对于单值的数据,每一个SPC的数据总量不要低于30个;如果是成组的数据,不要低于每组5个,至少20个子组,这样才具有统计学意义。
以下分享课件PPT图片
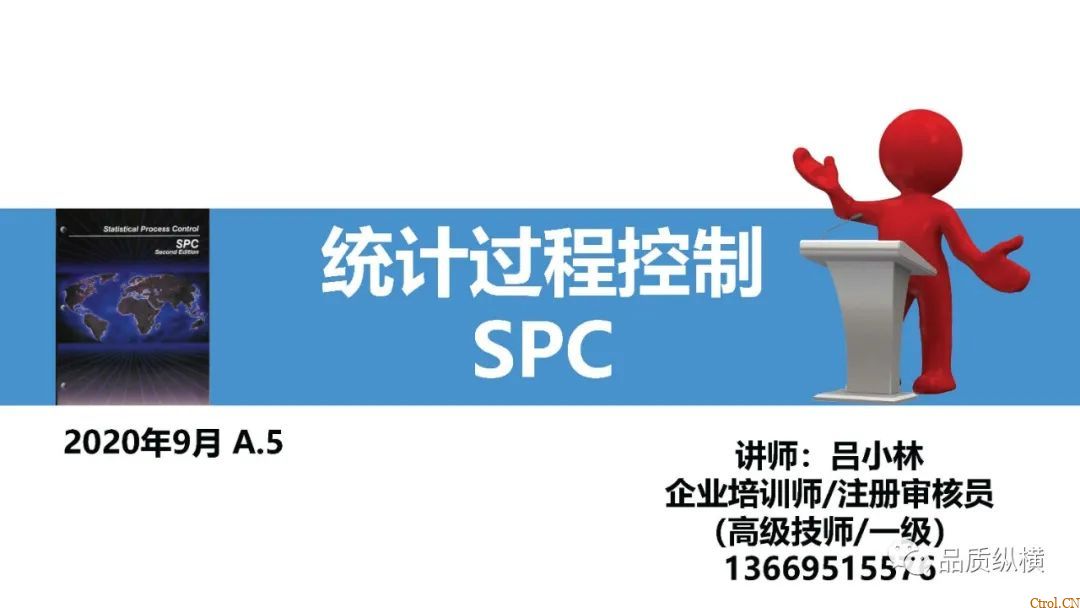
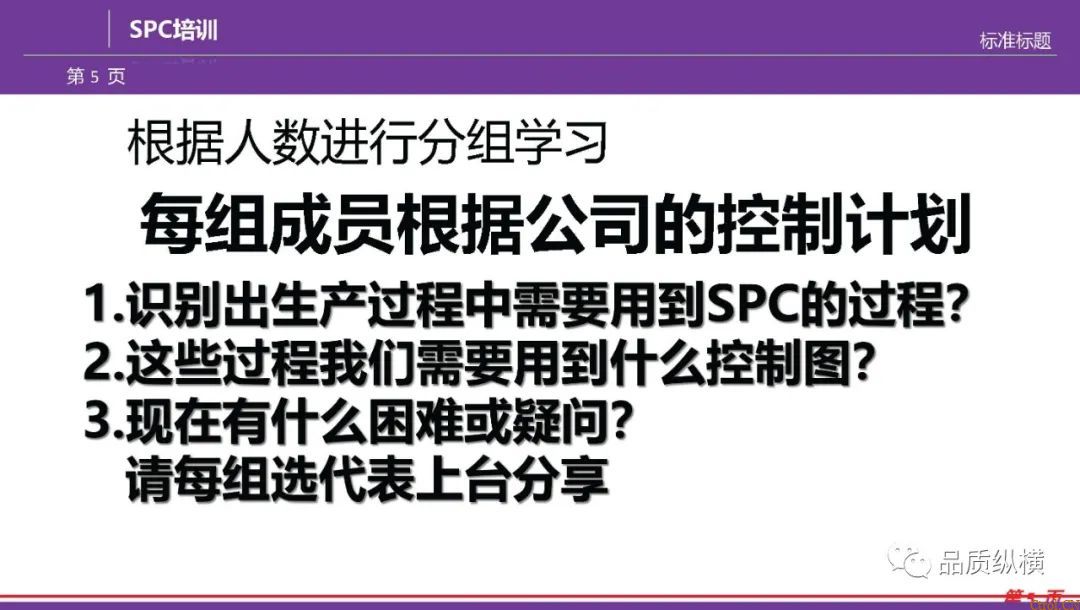
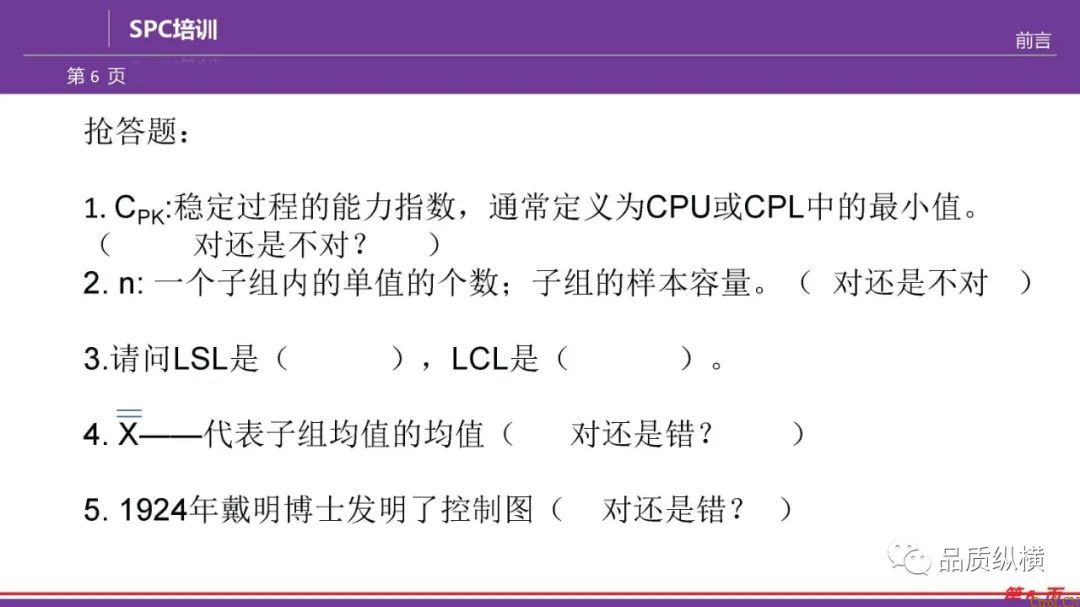
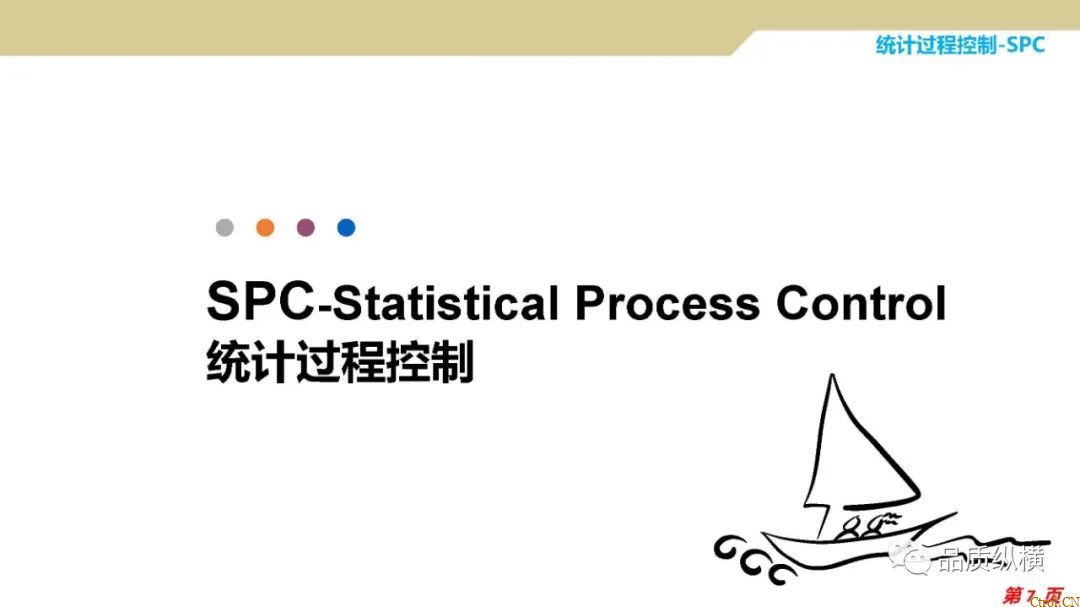
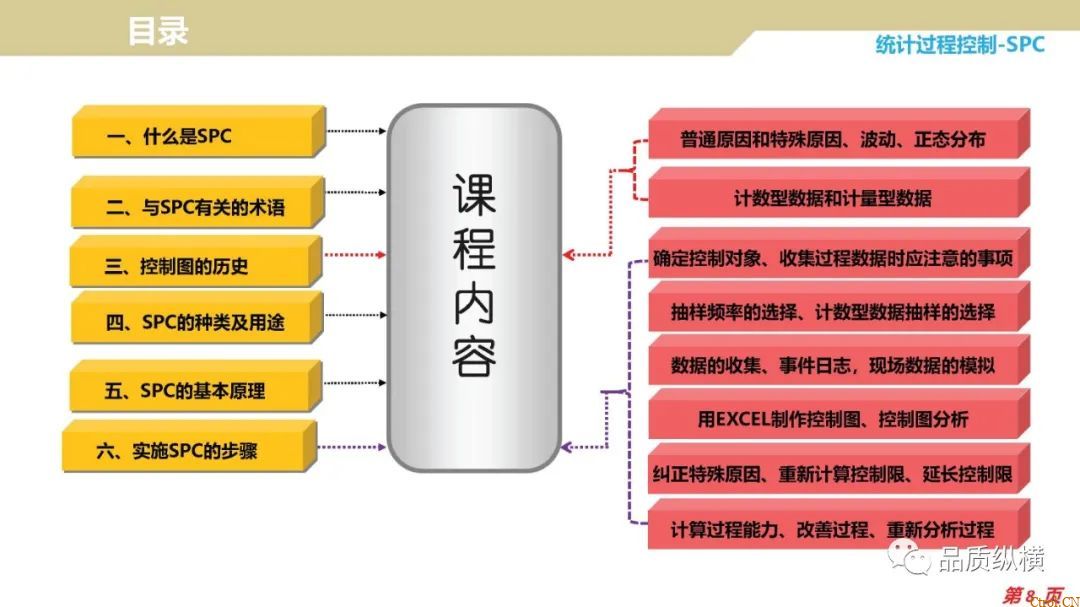
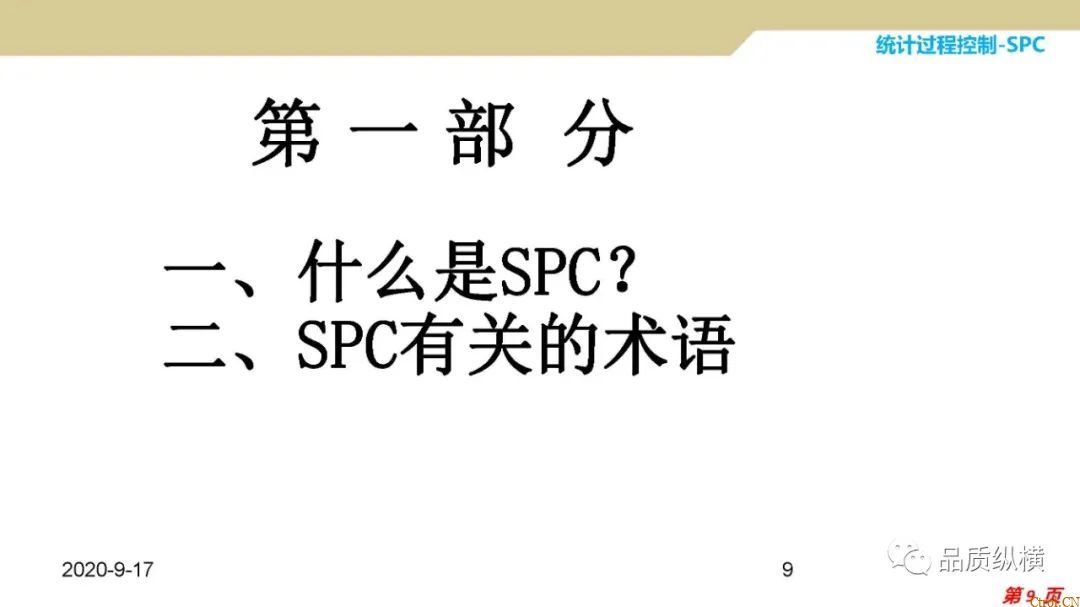
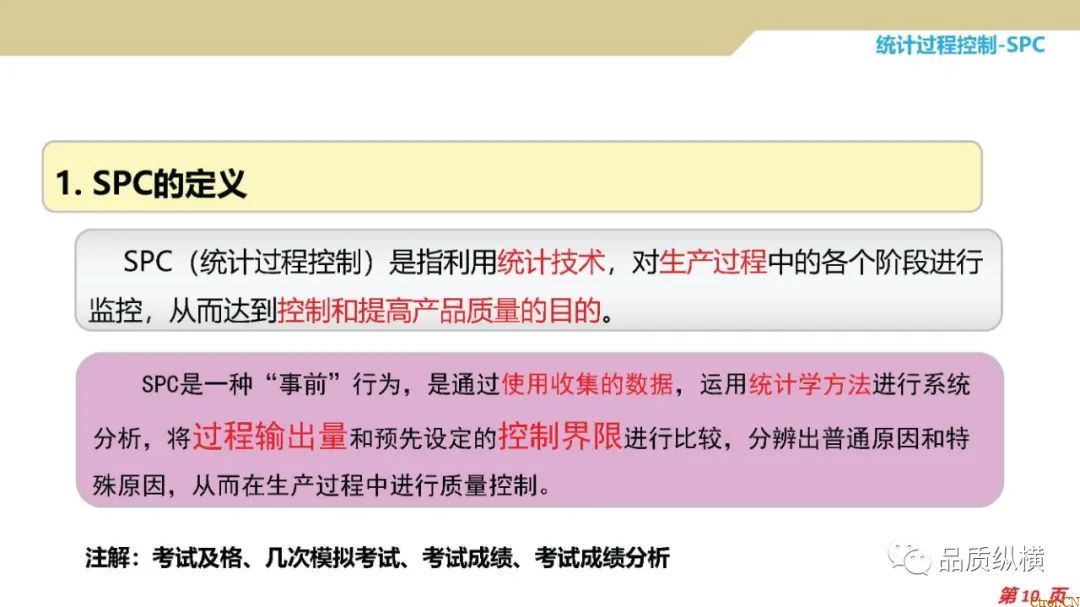
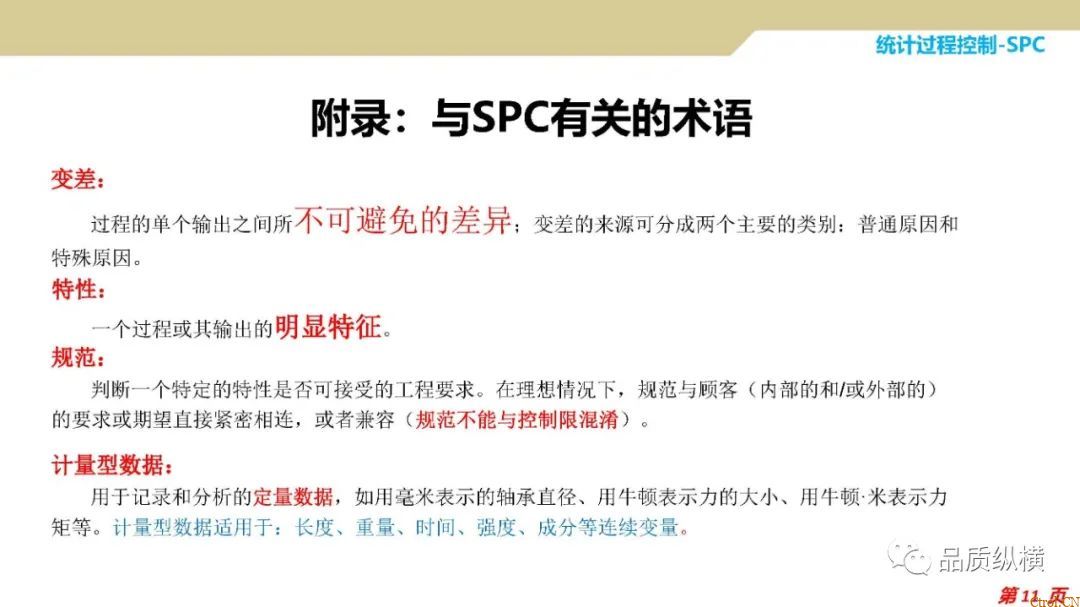
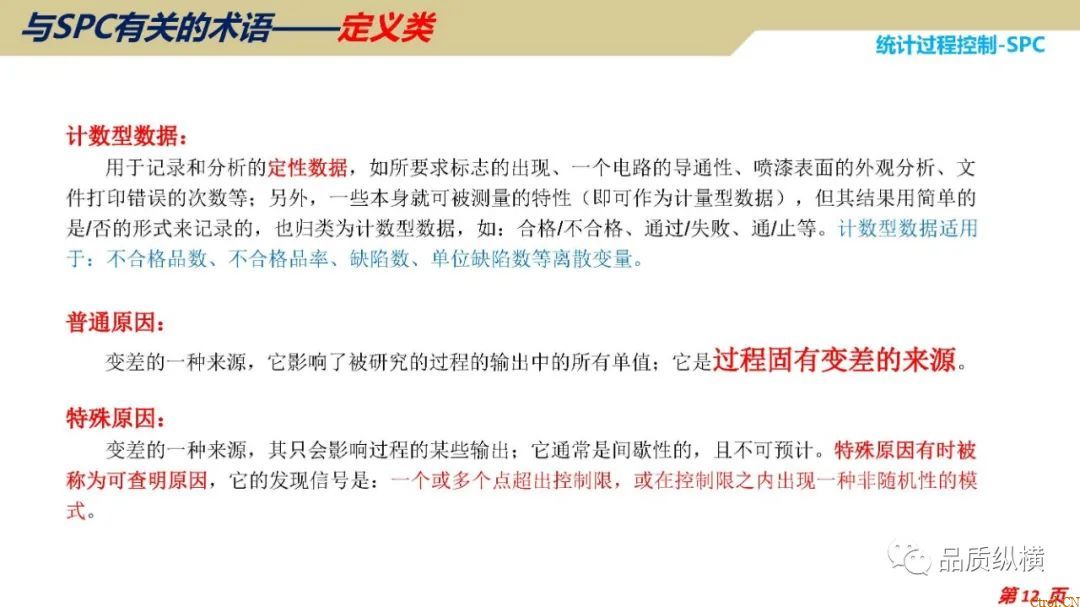
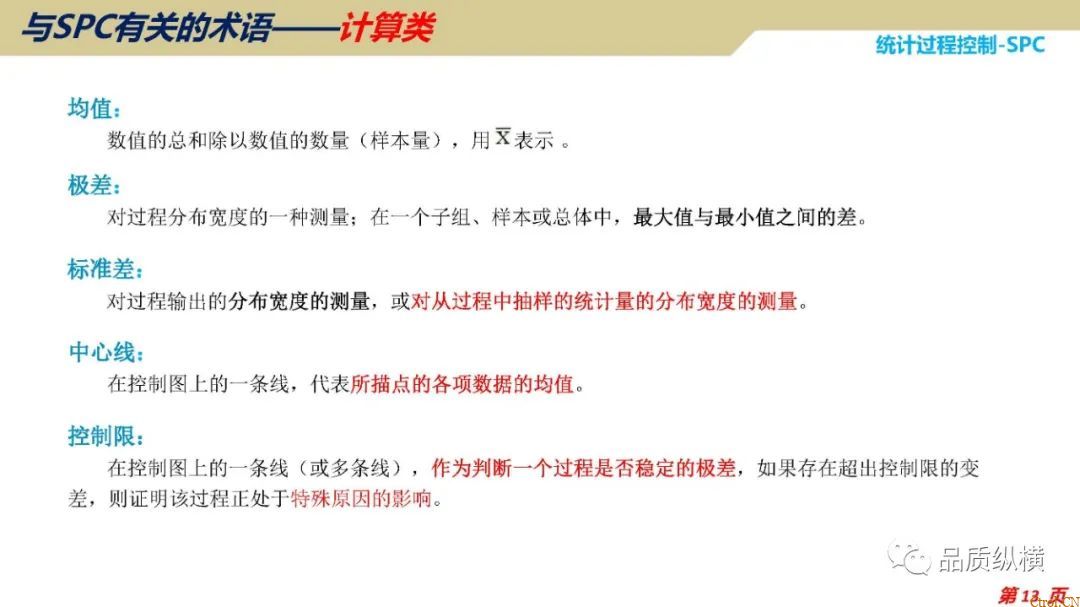
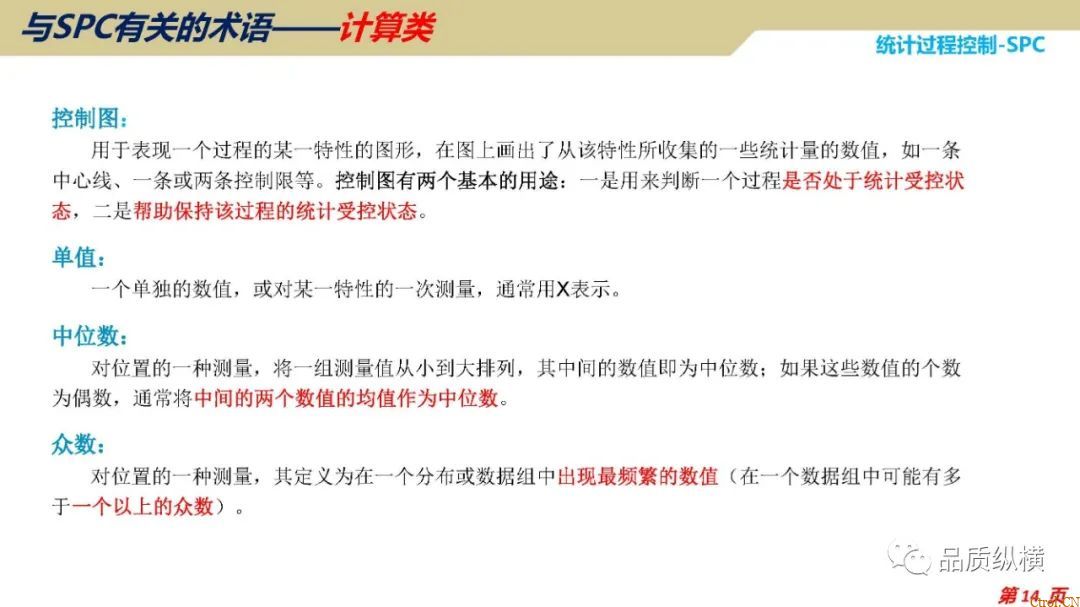
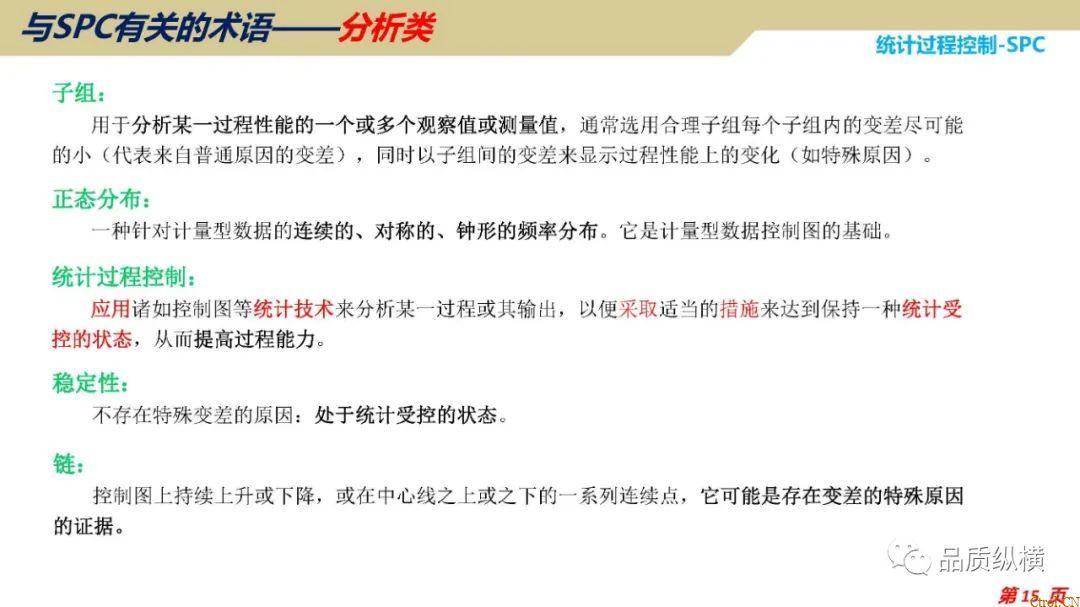
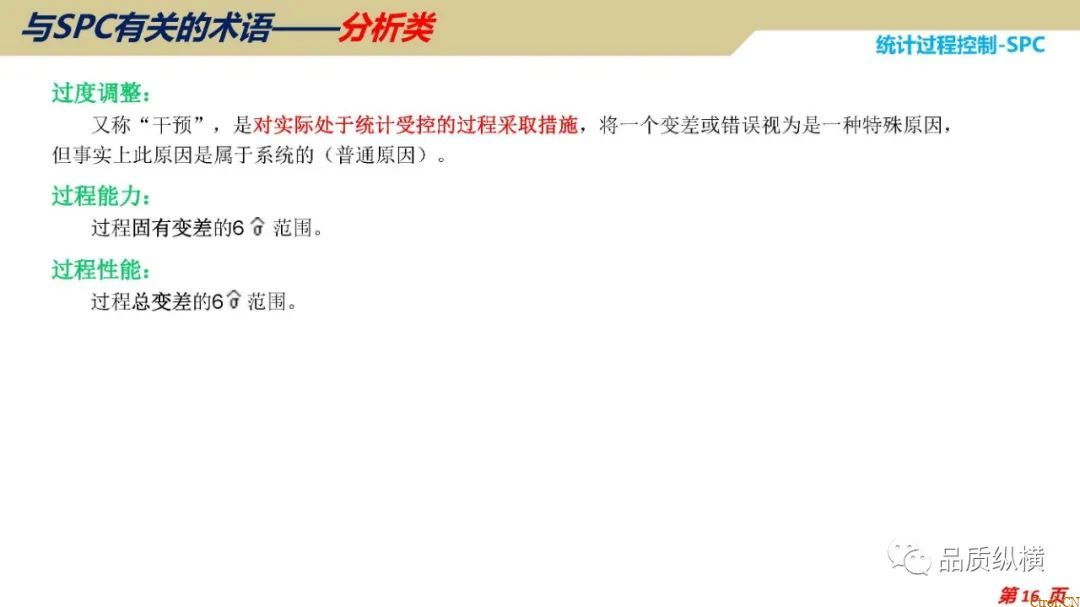
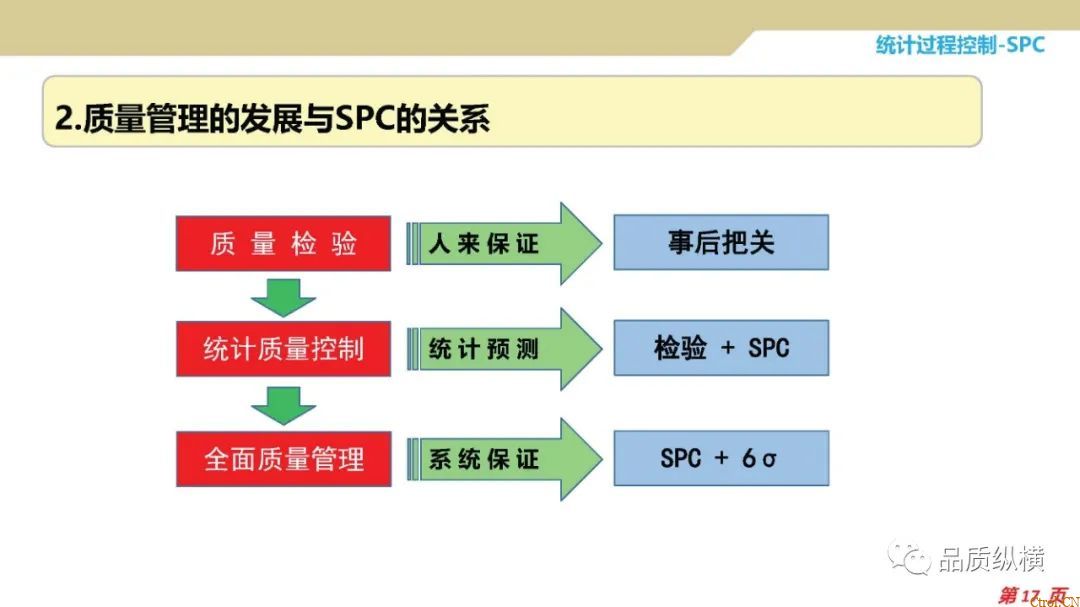
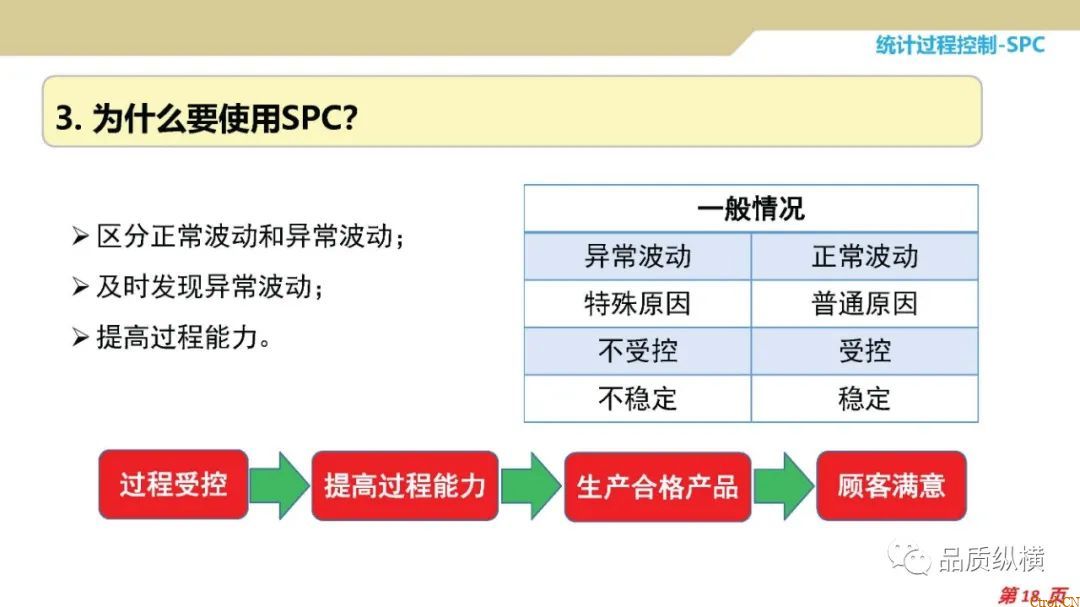
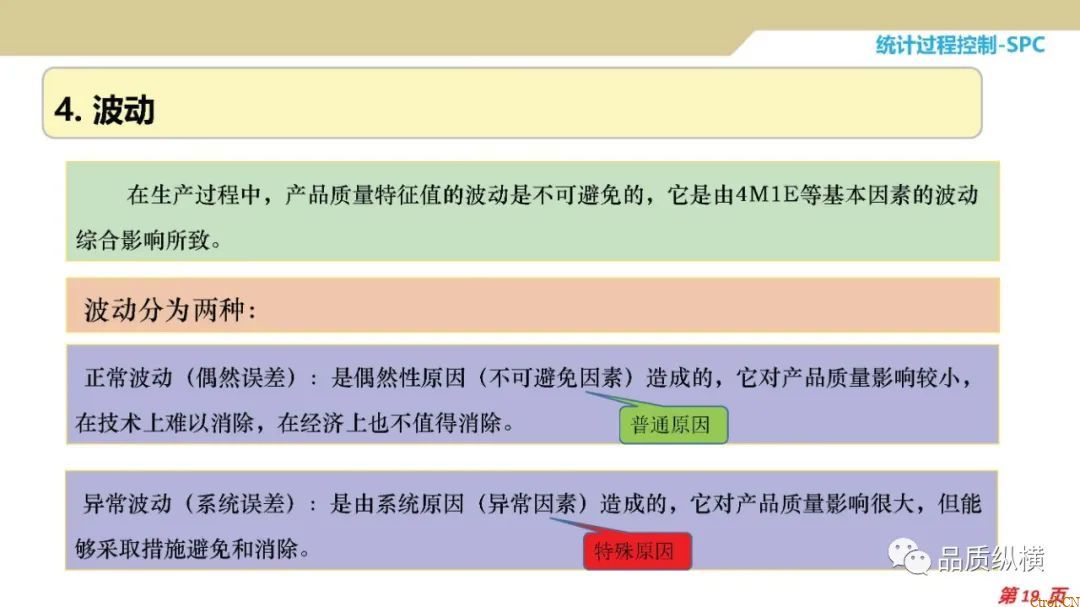
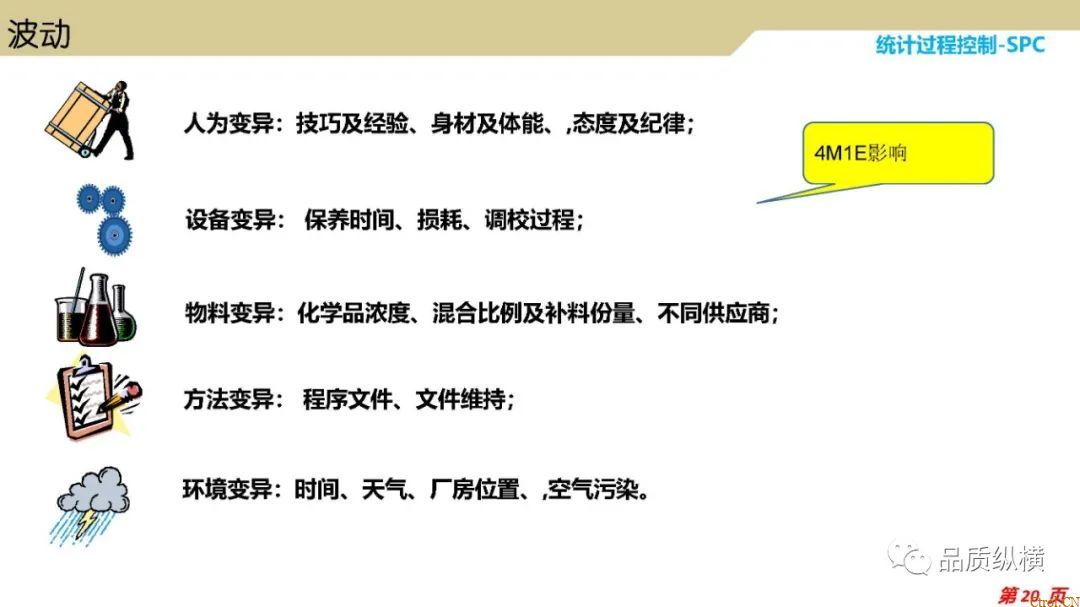
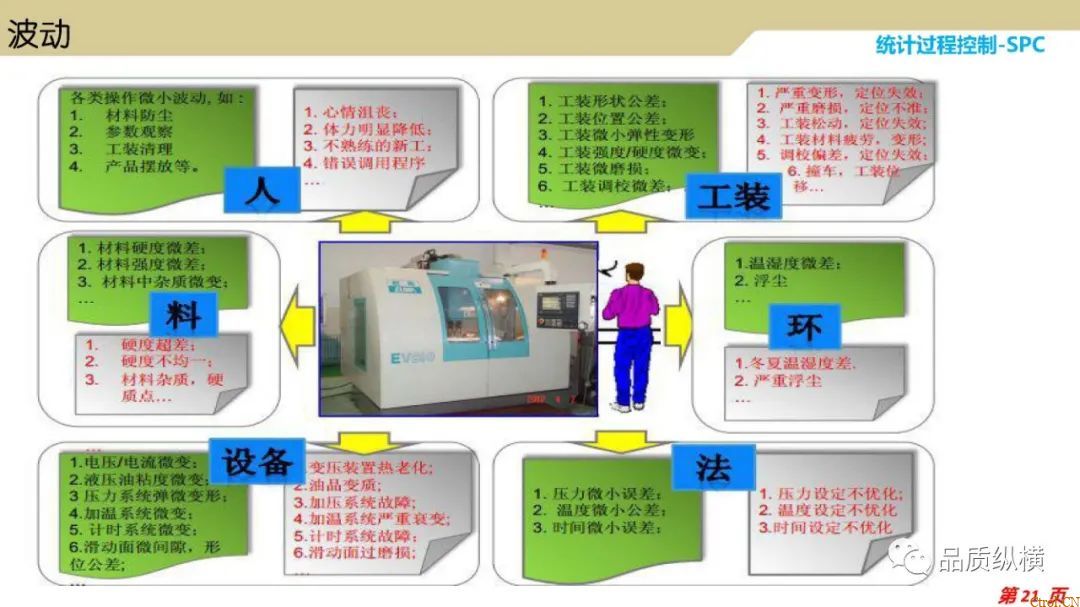
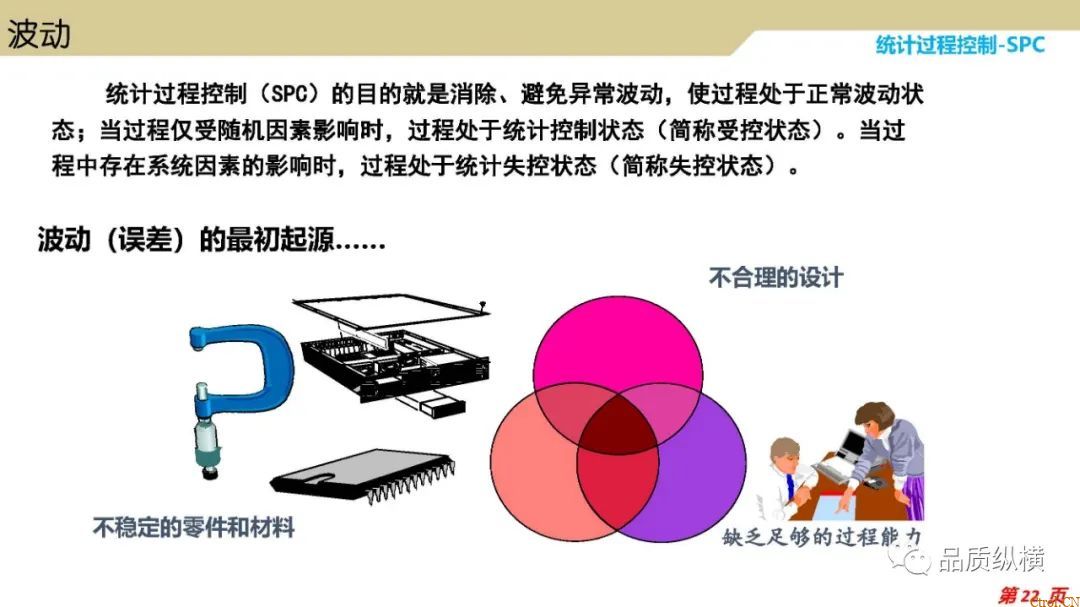
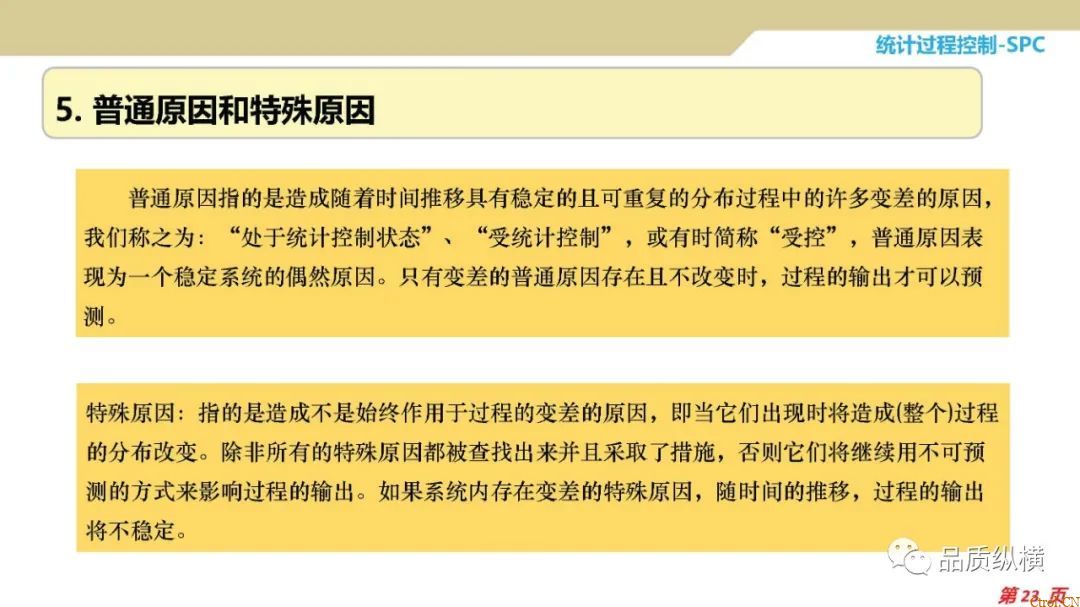
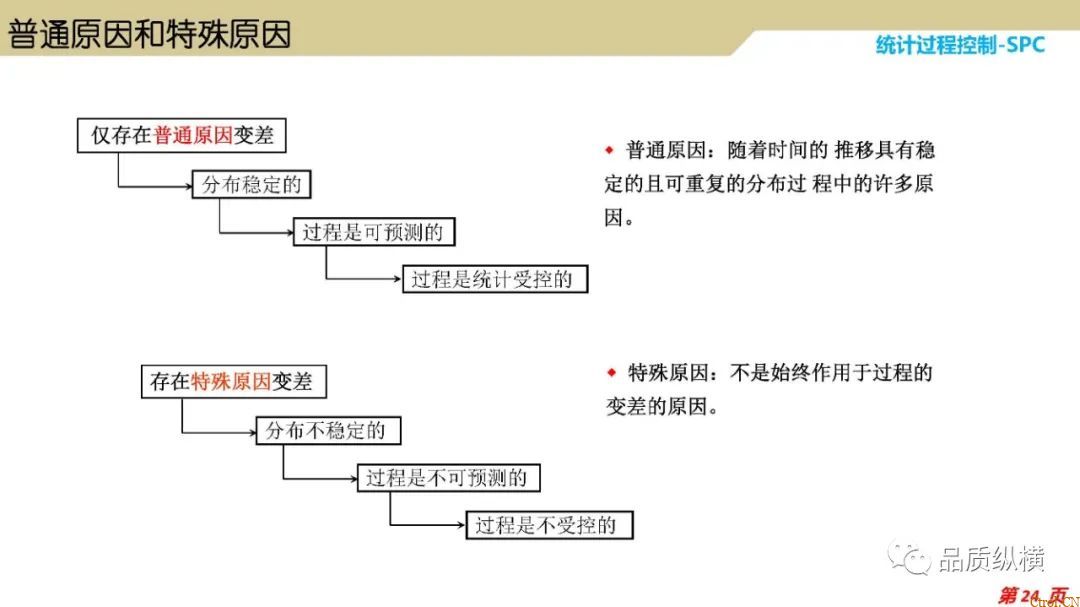
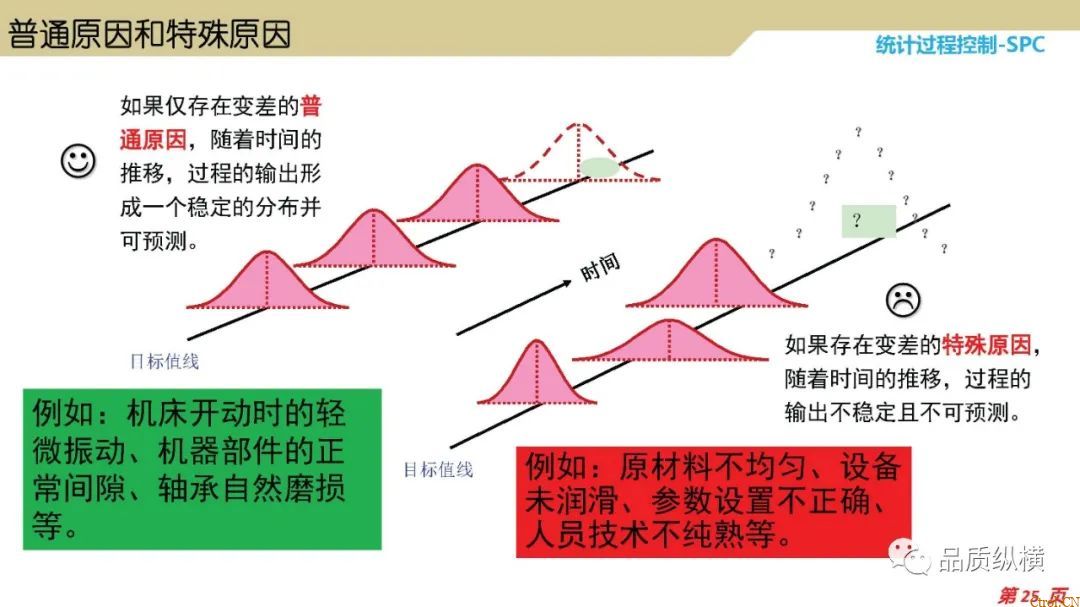
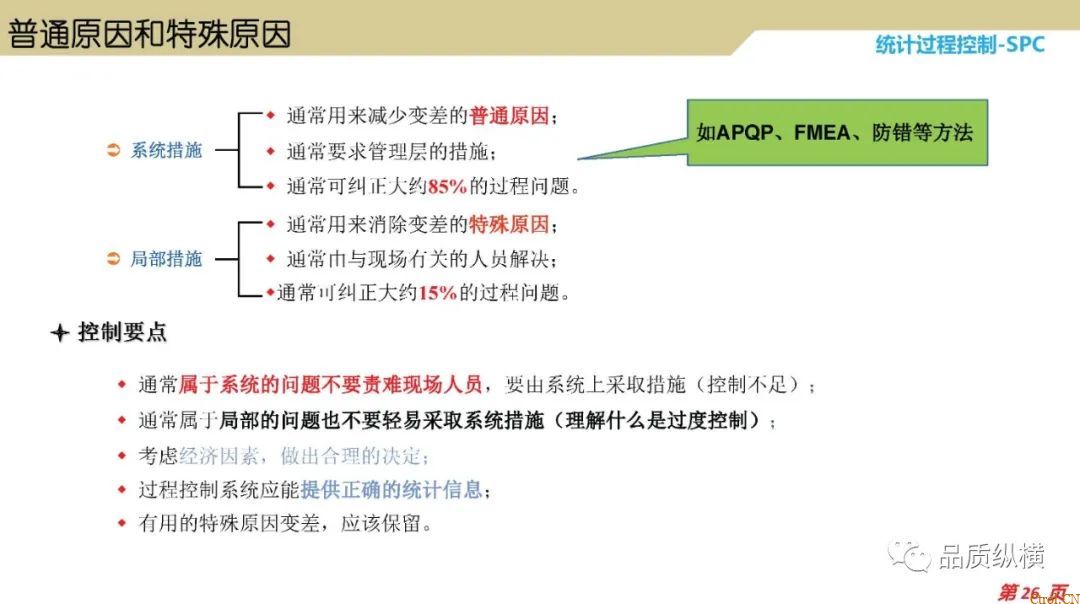
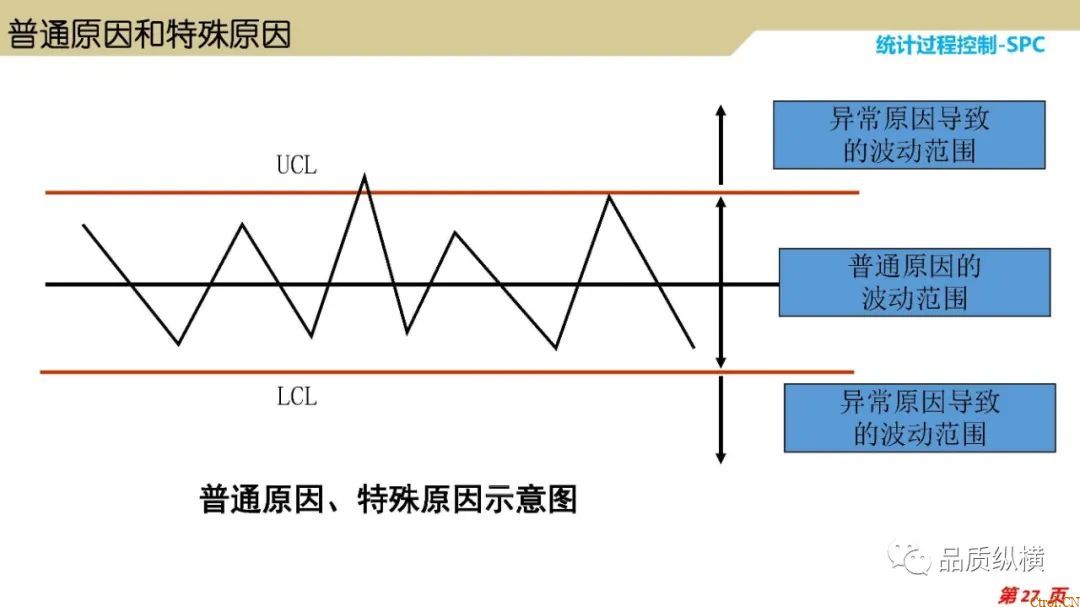
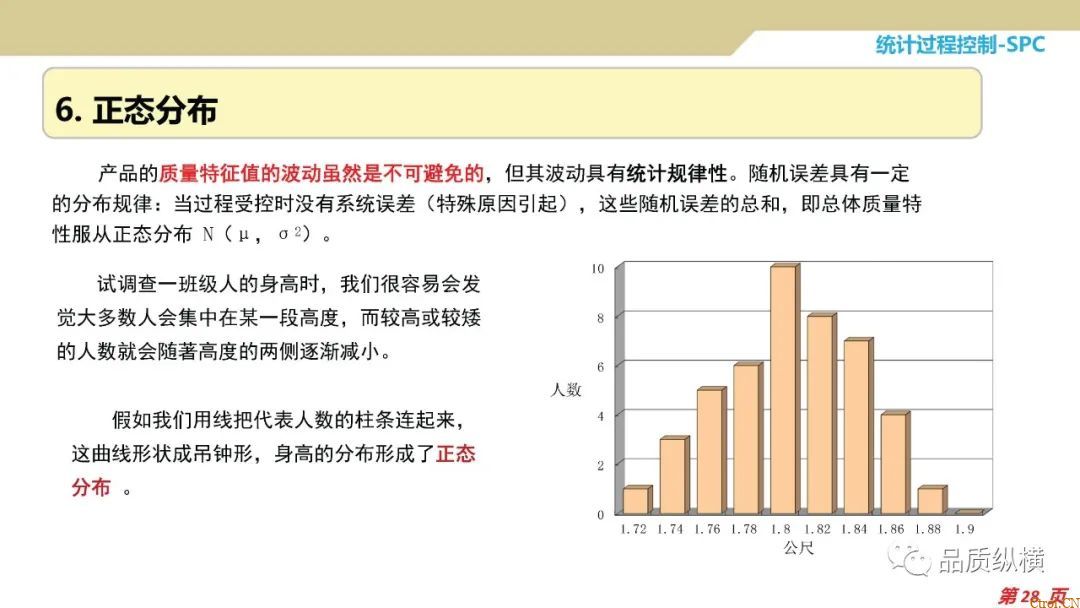
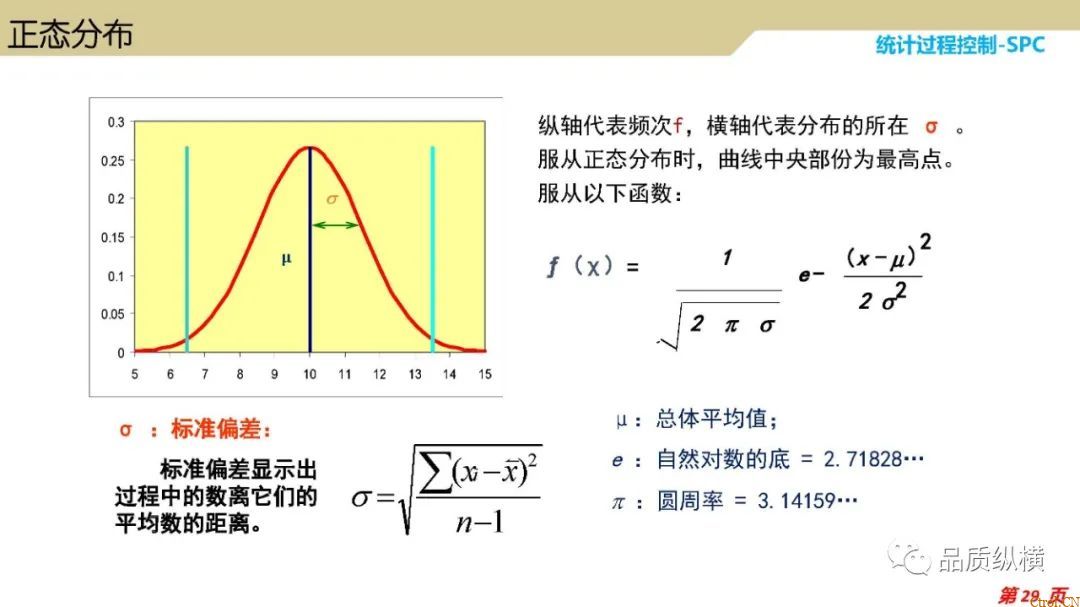
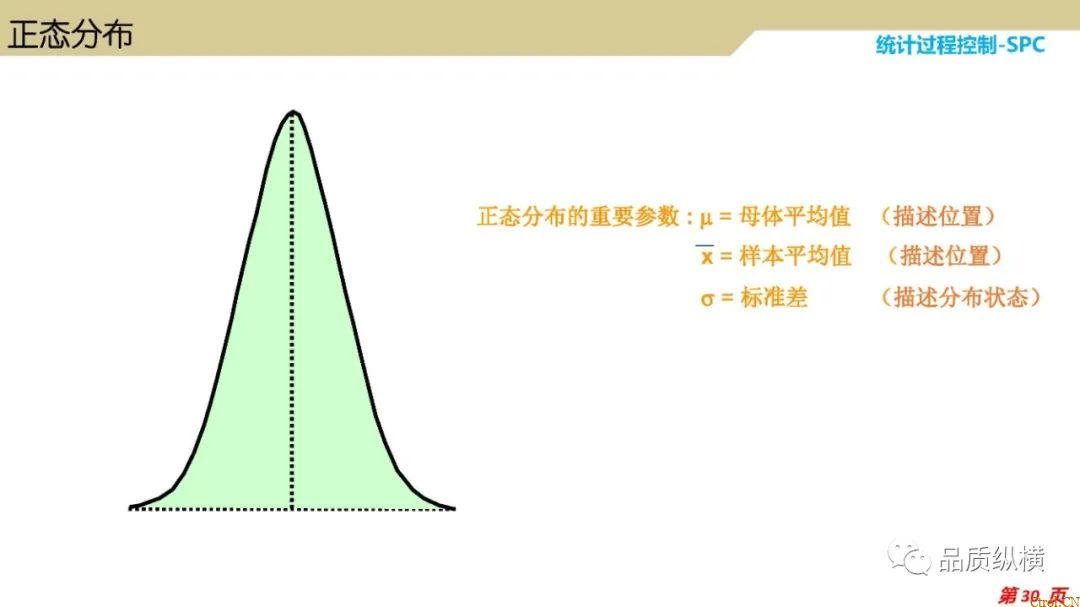
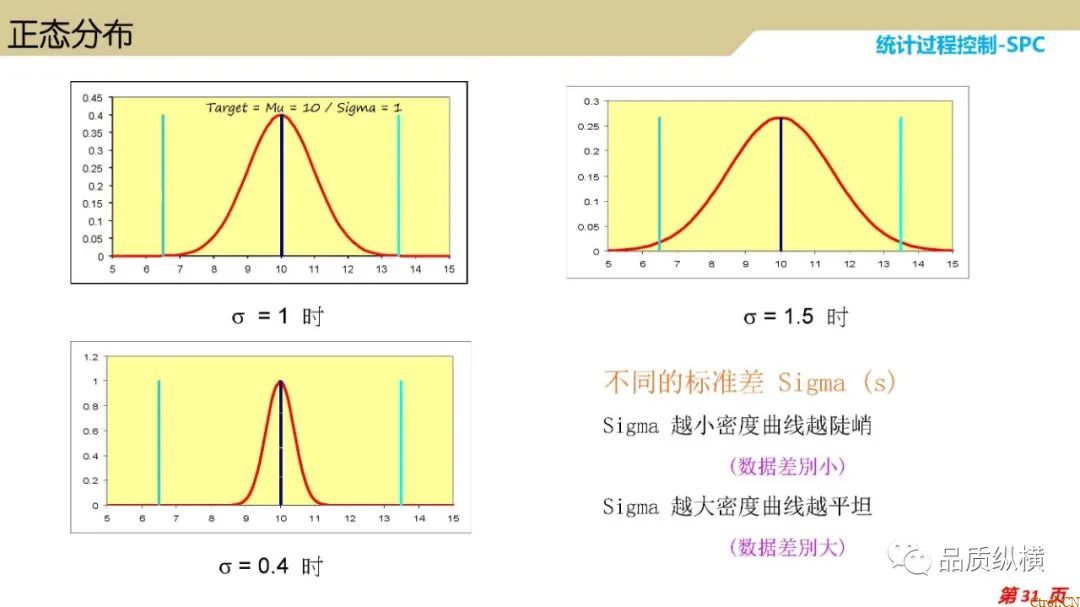
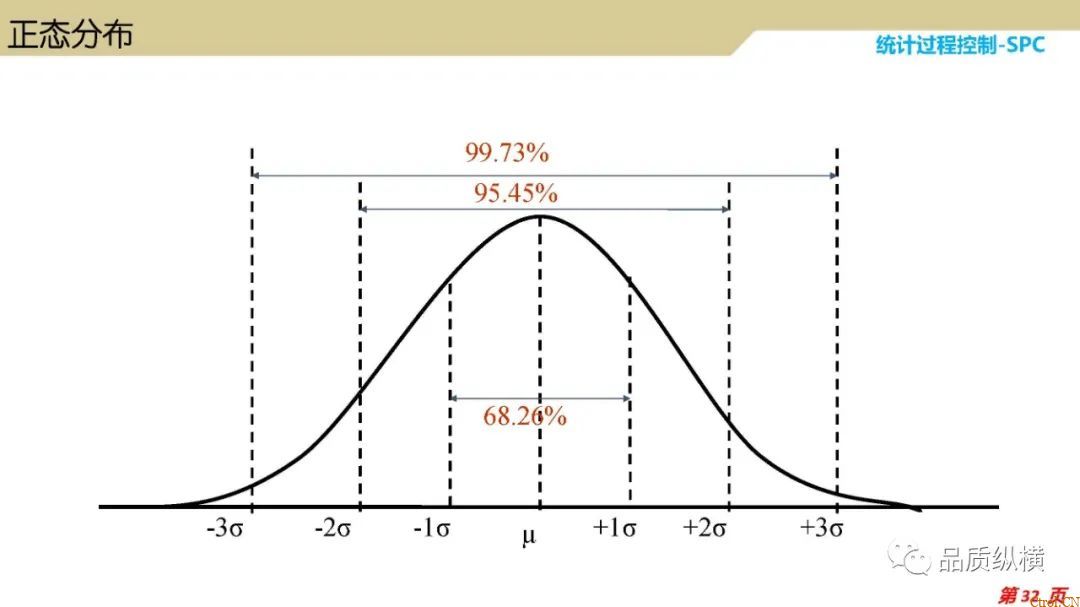
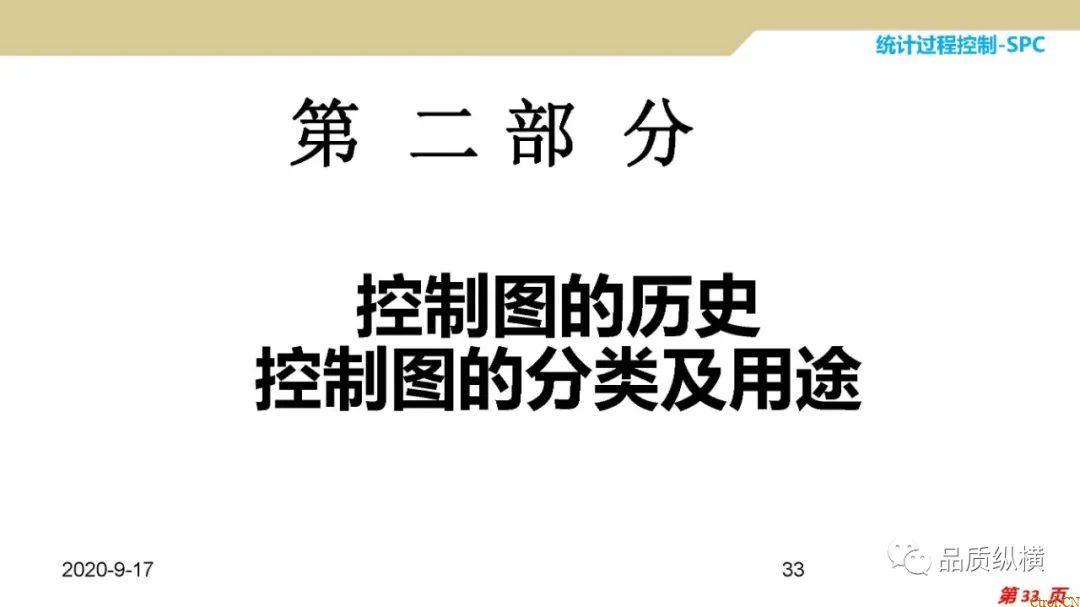
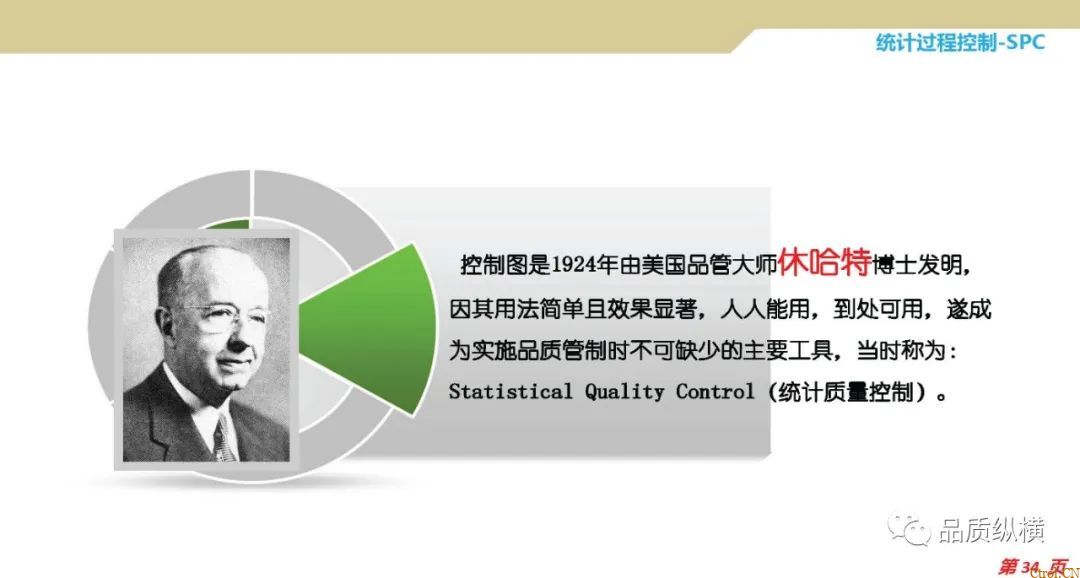
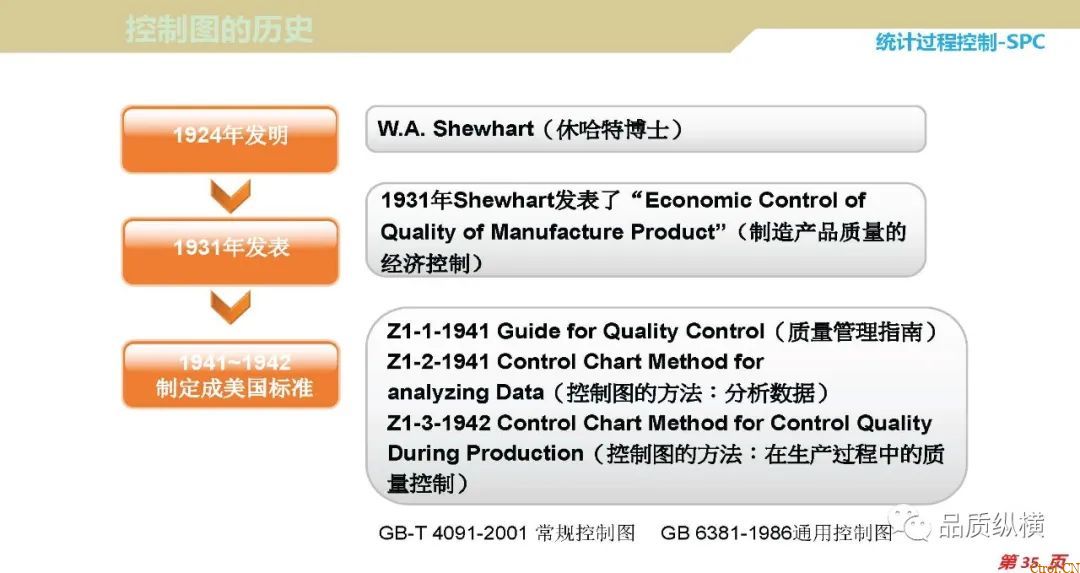
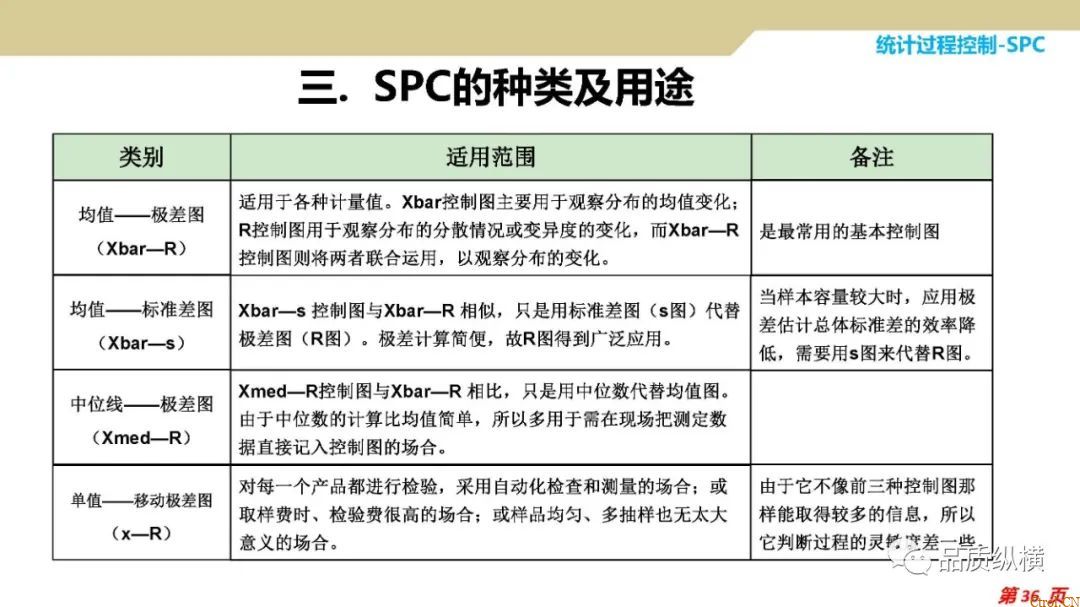
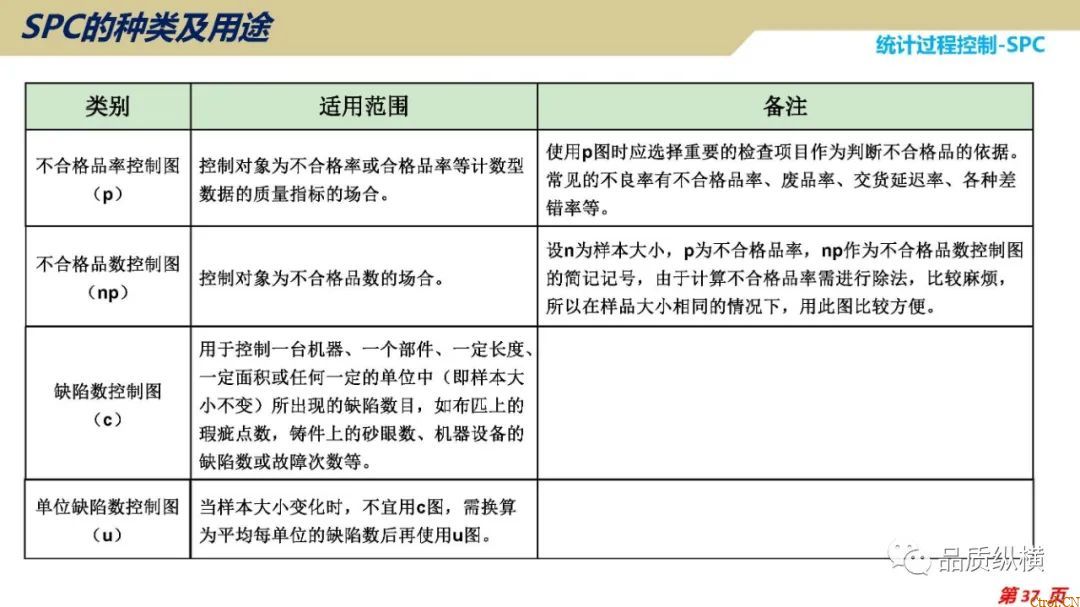
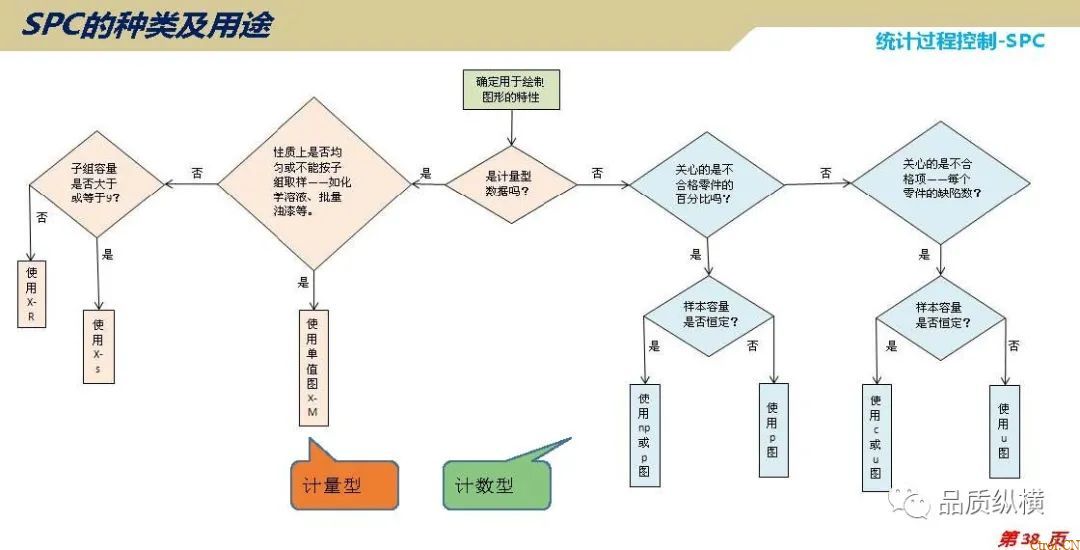
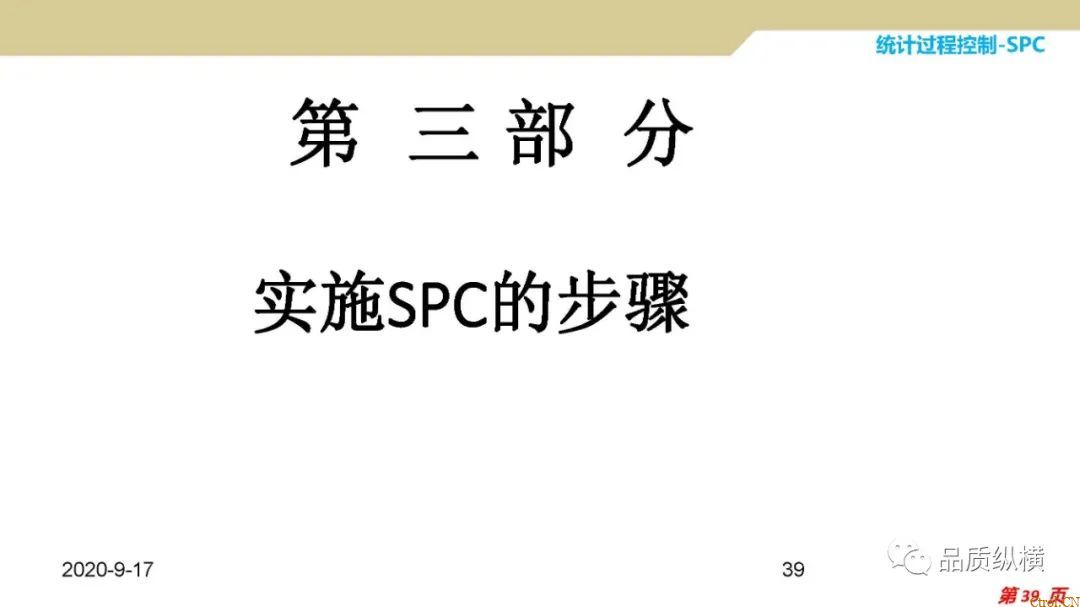
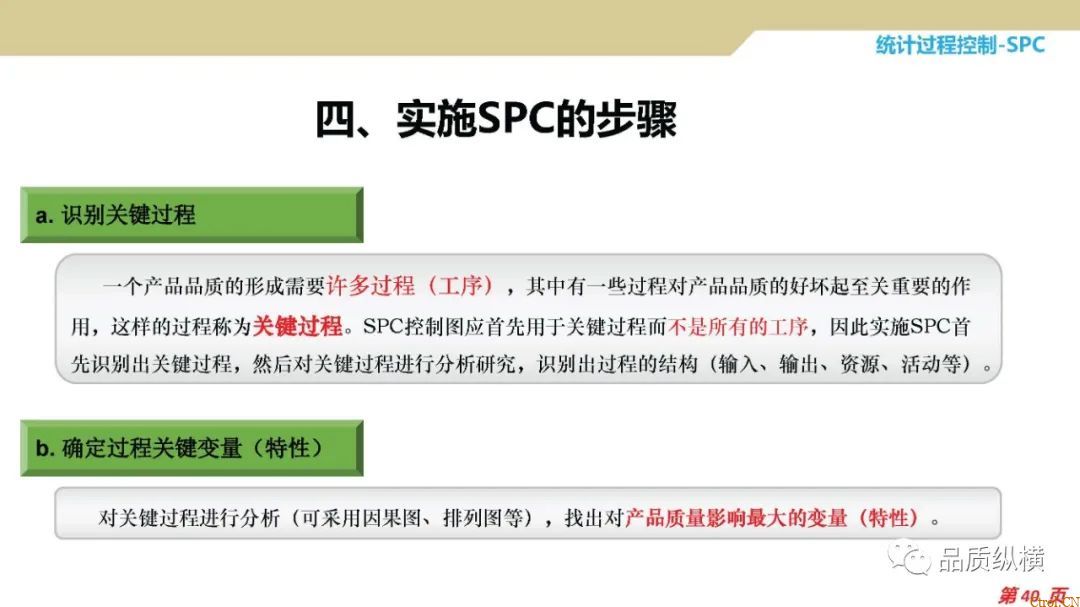
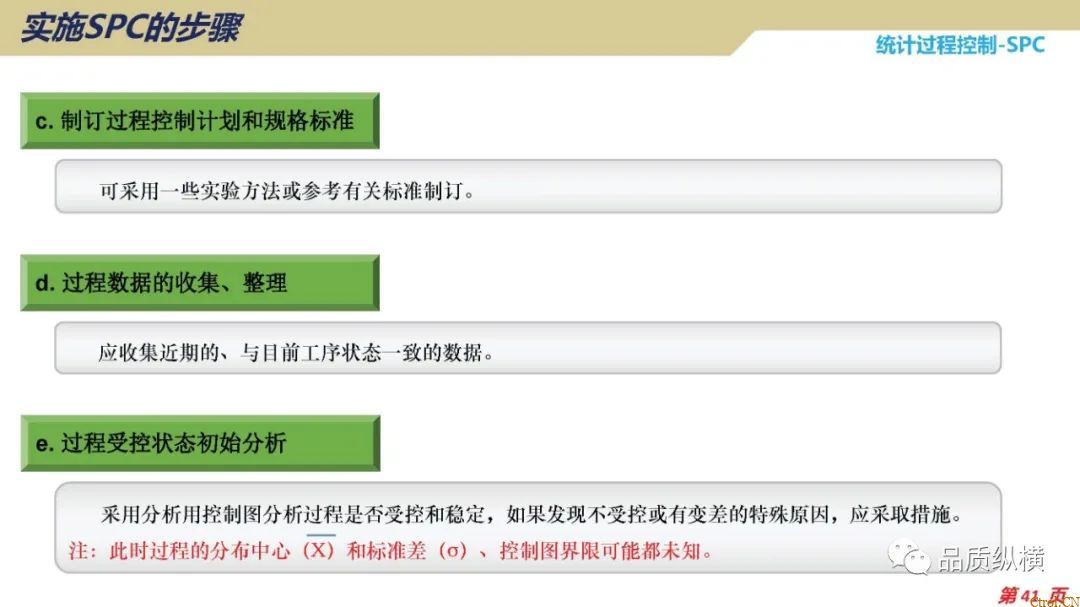
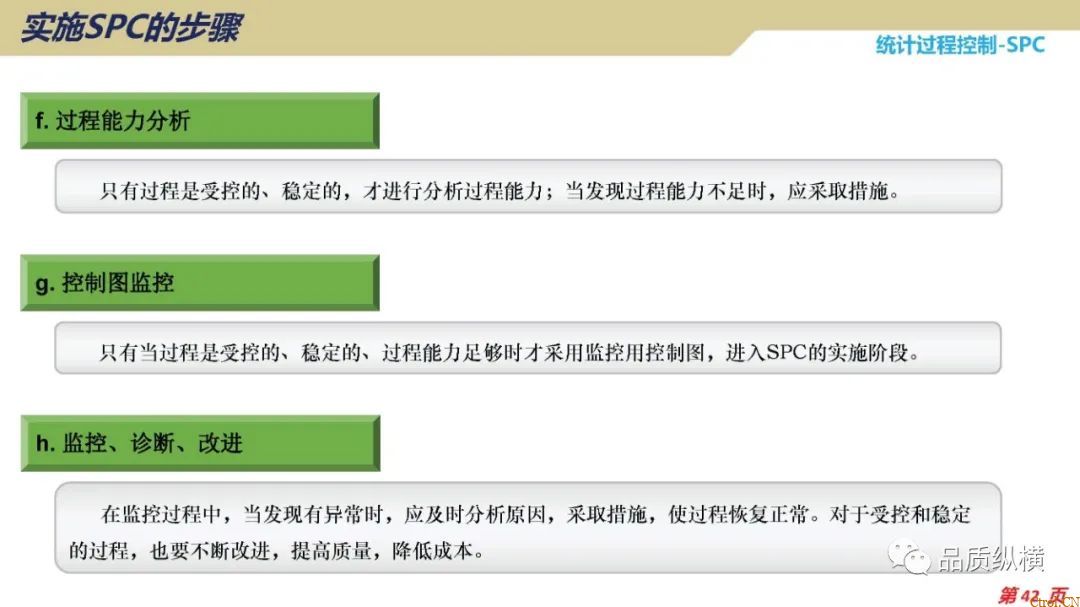
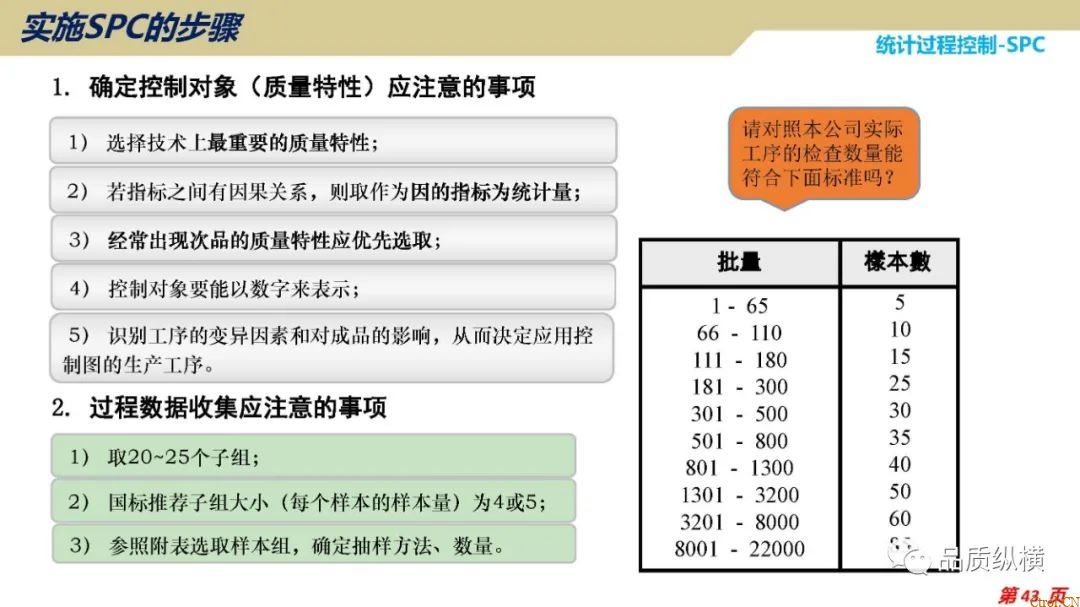
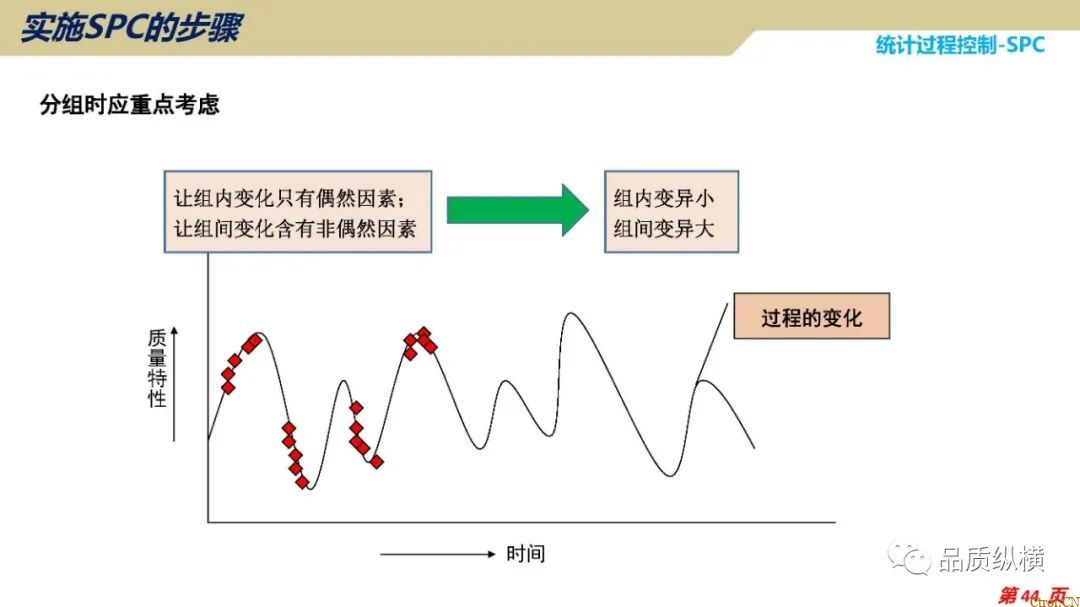
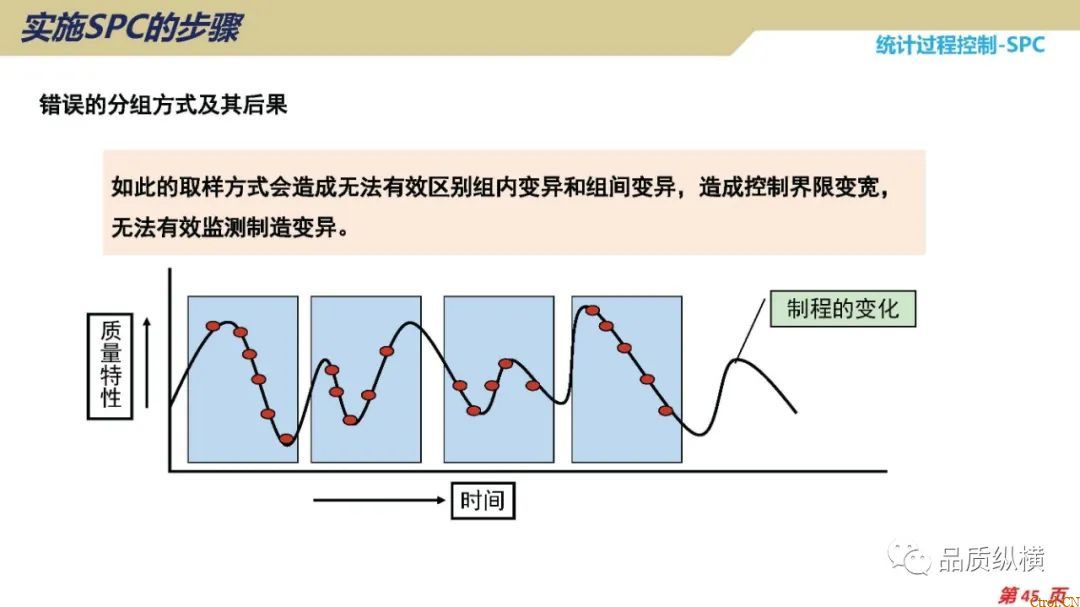

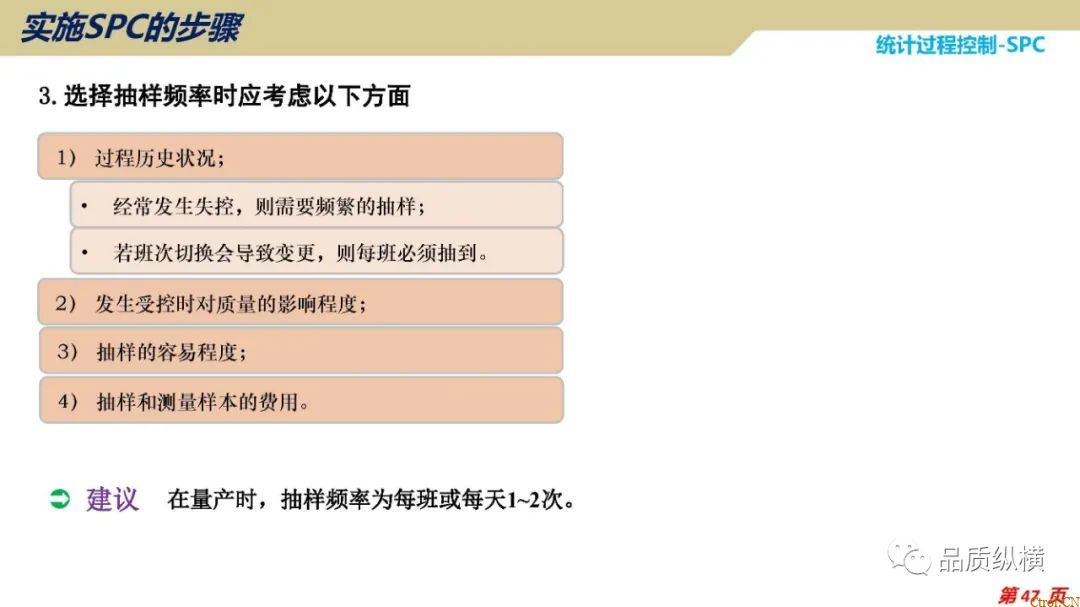
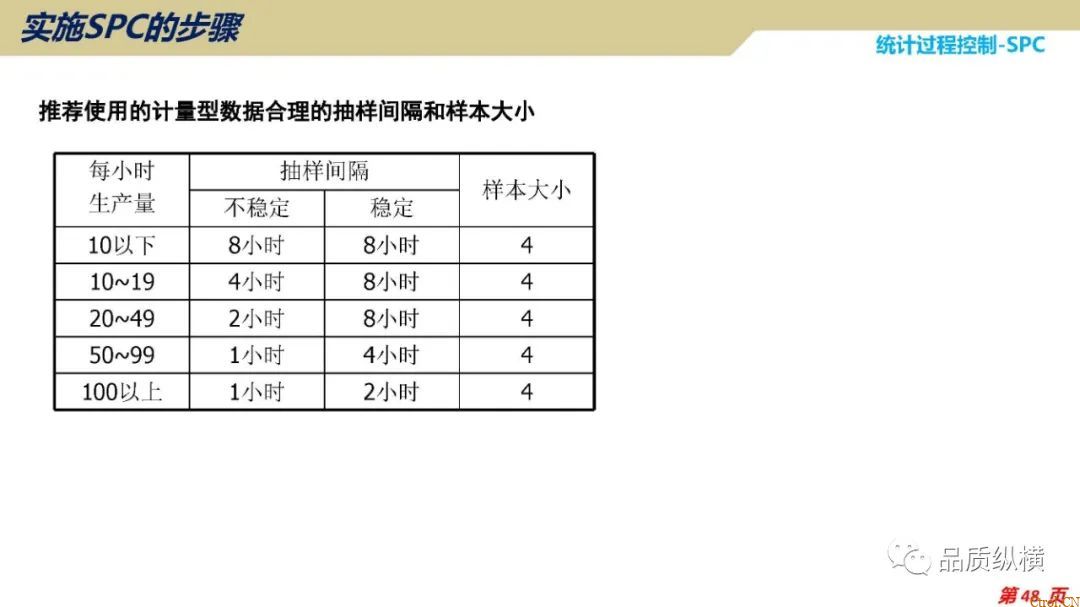
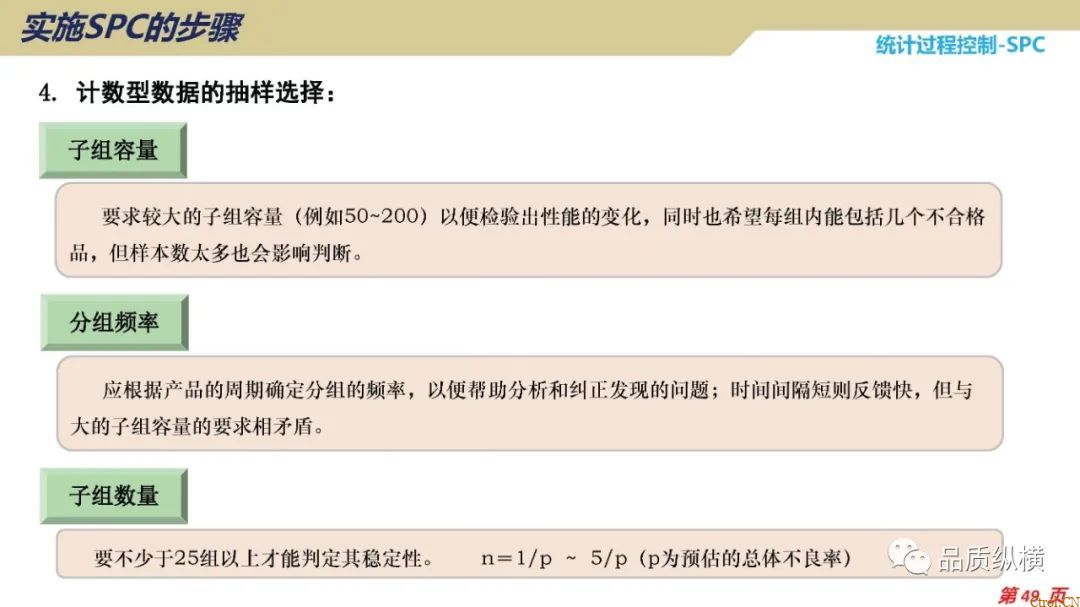
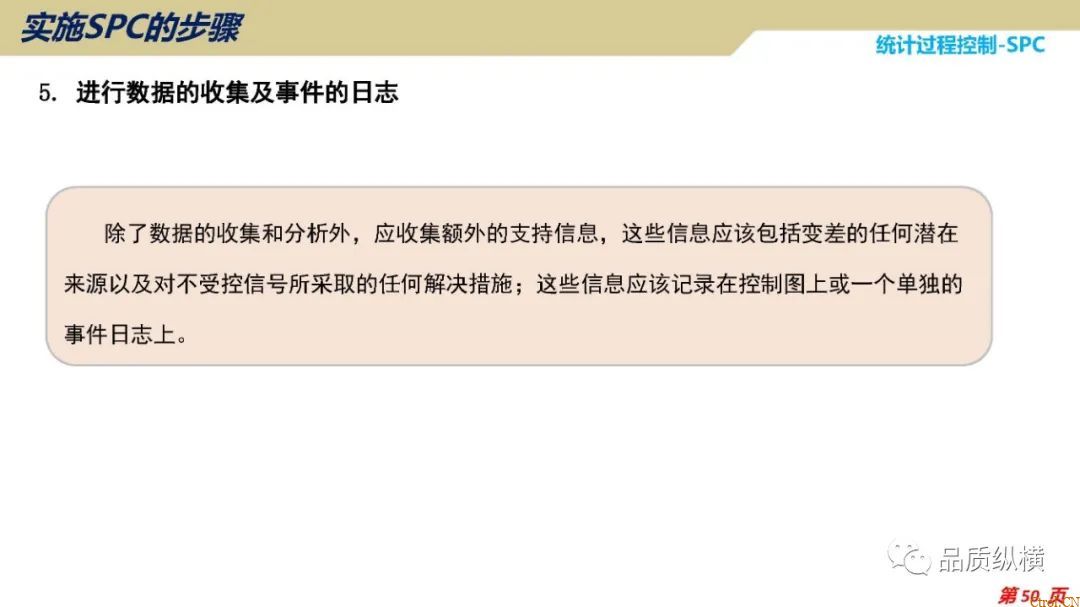
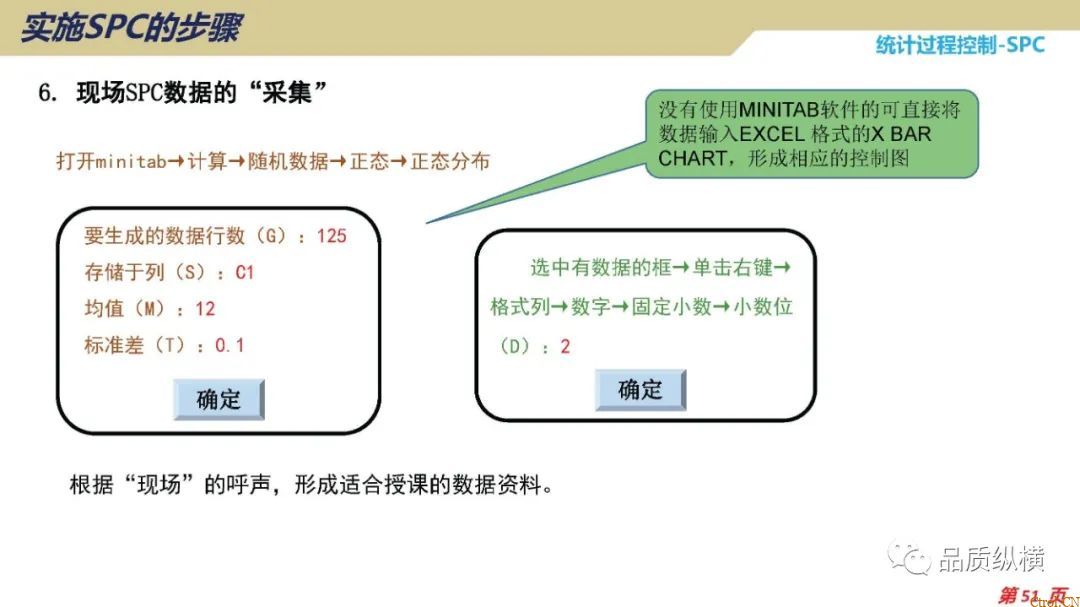
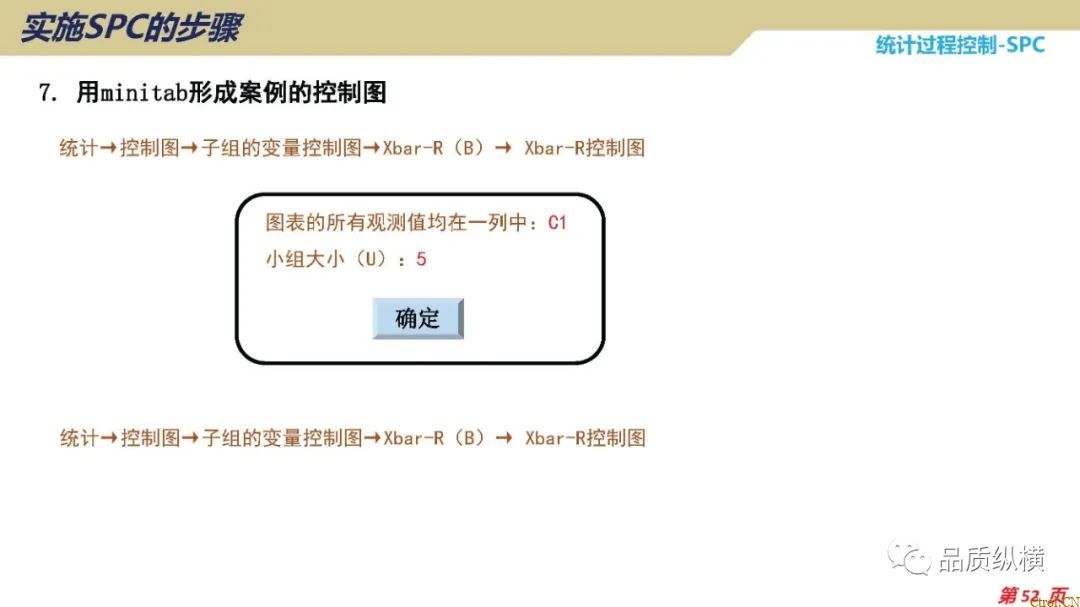
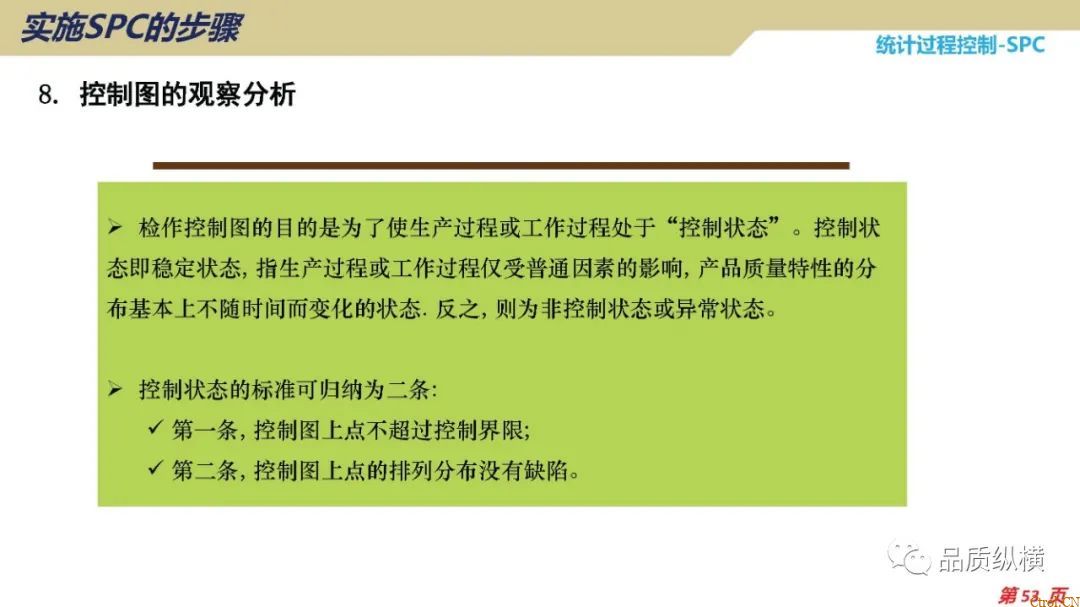
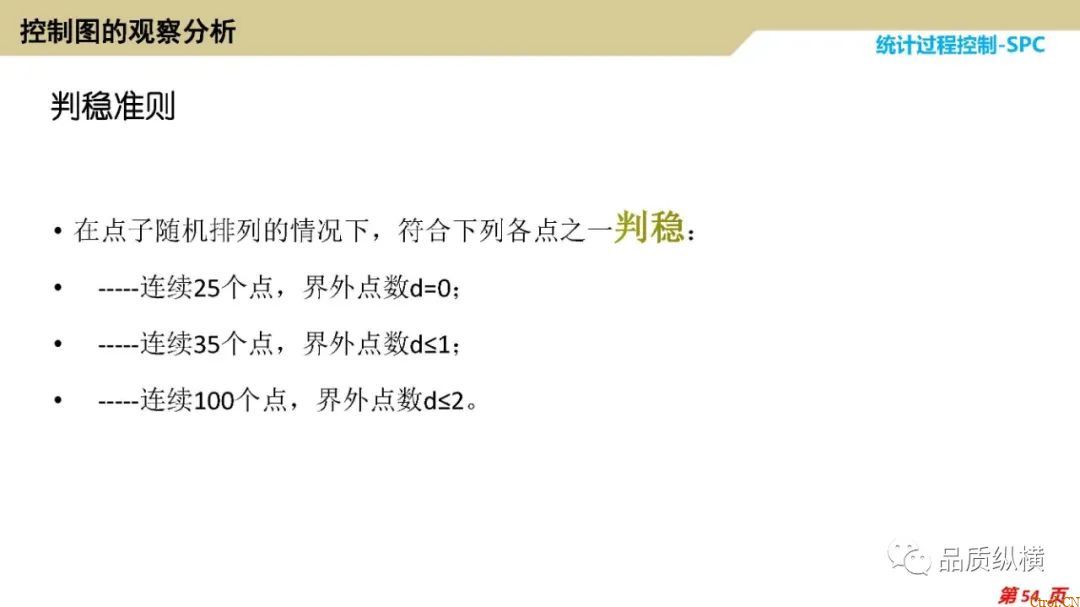
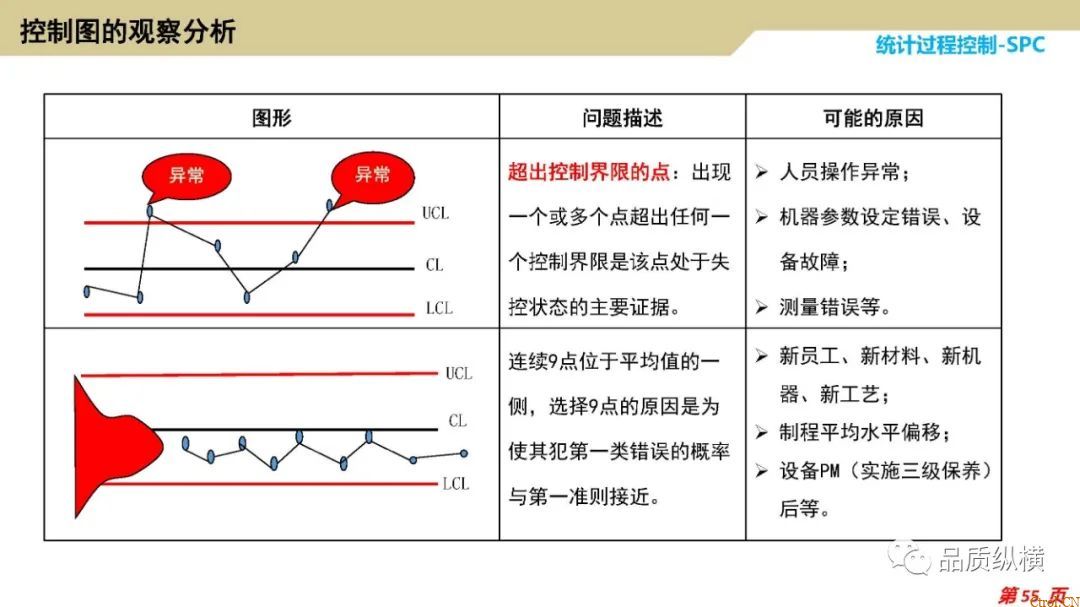
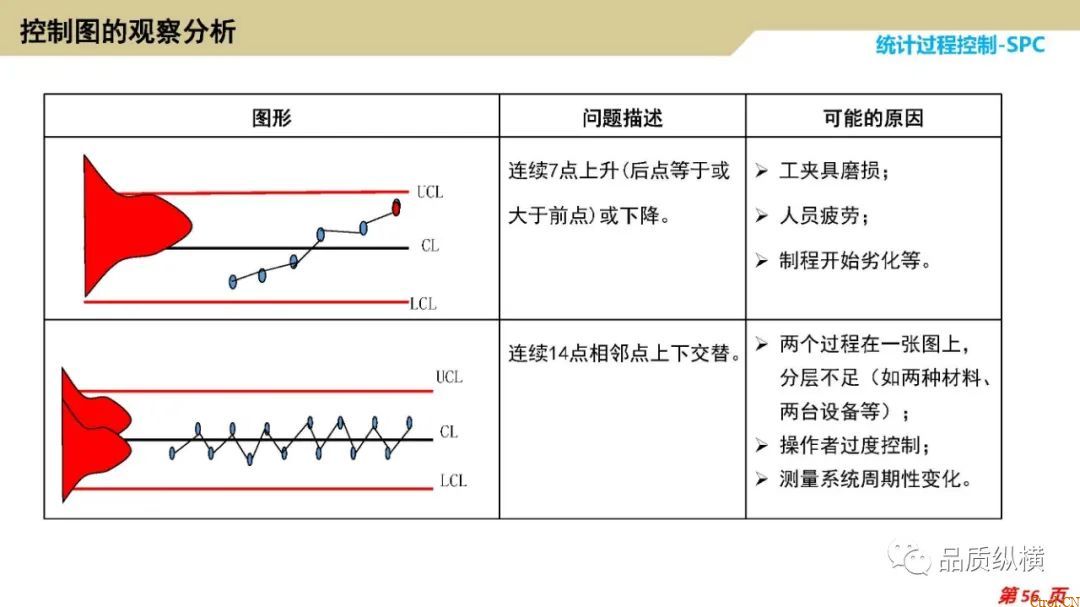
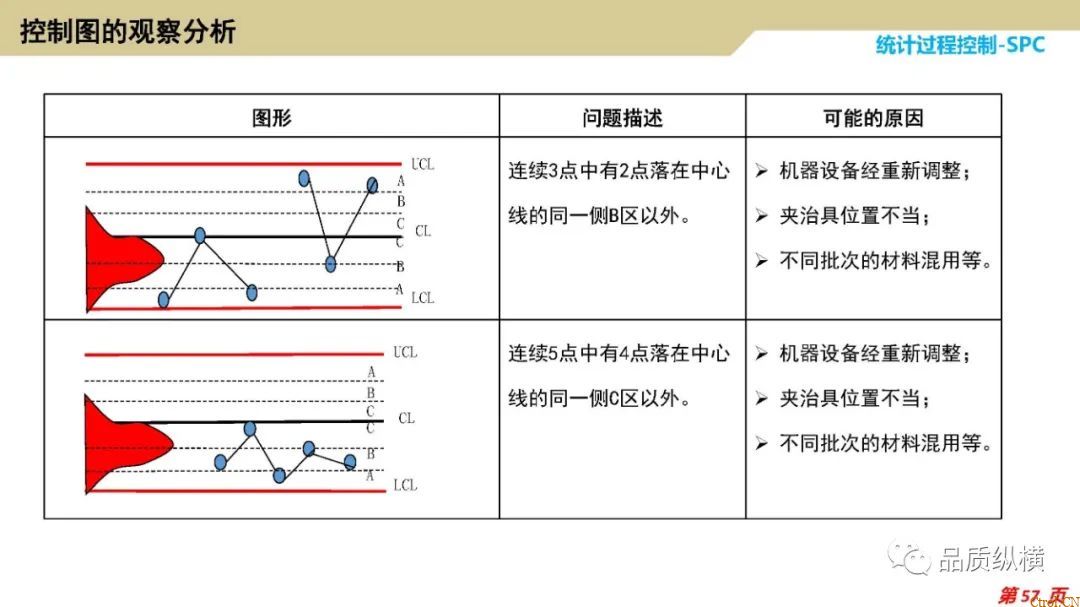
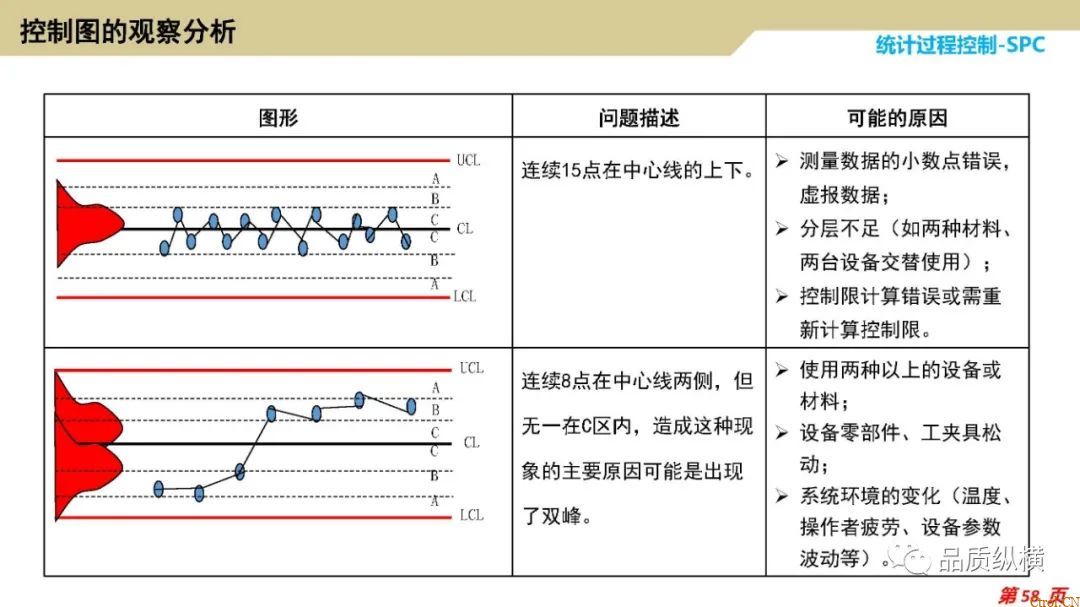
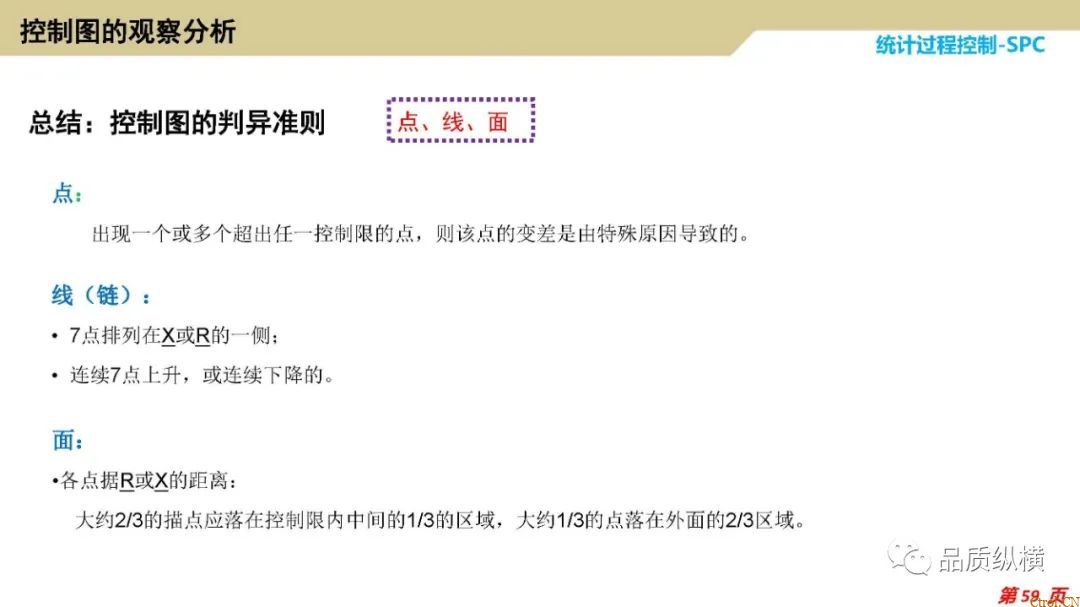
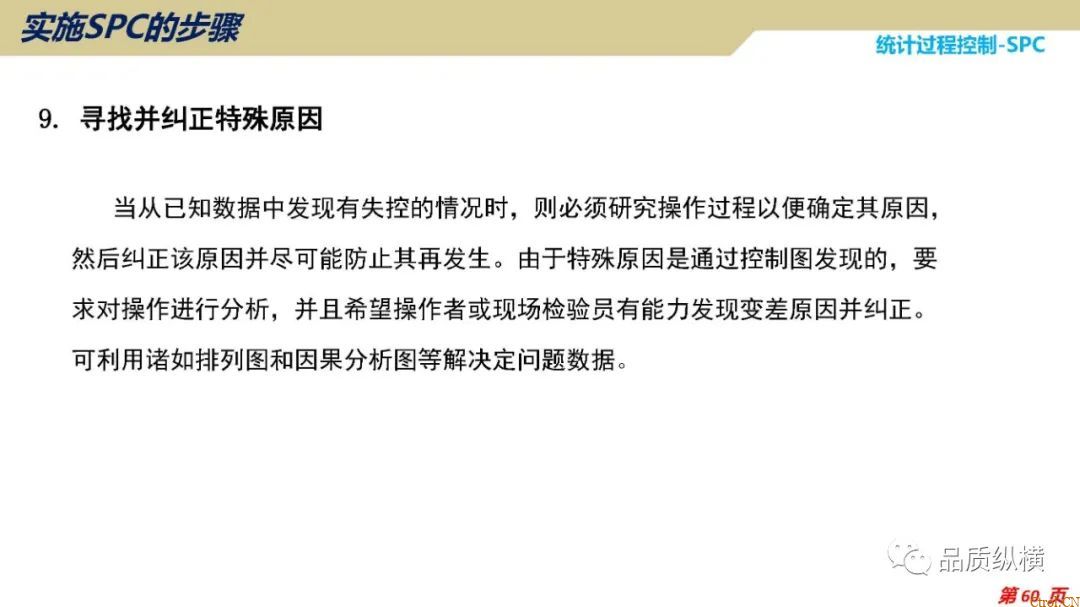
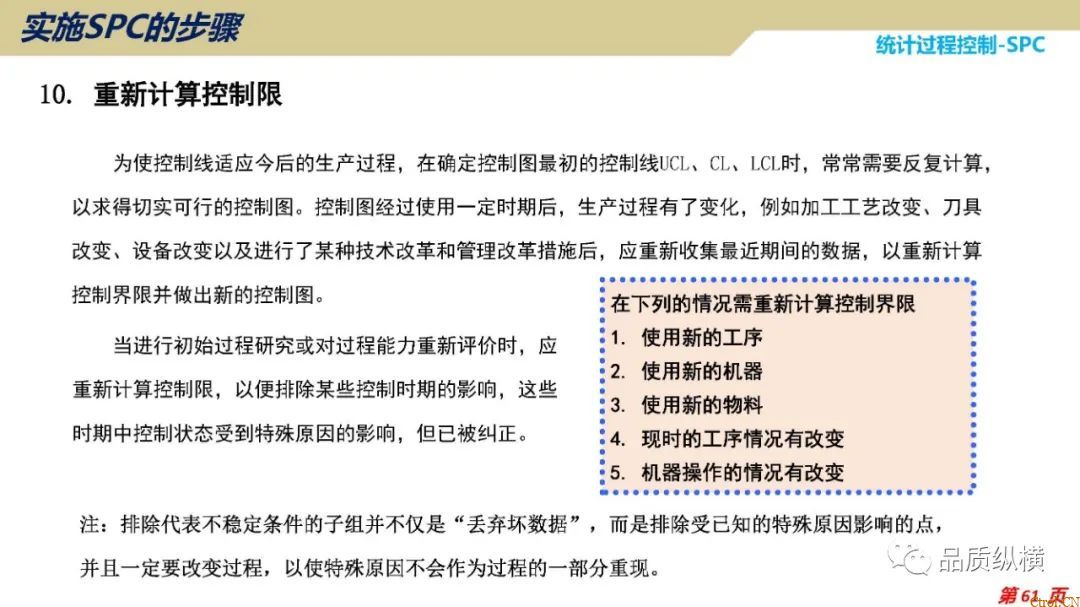
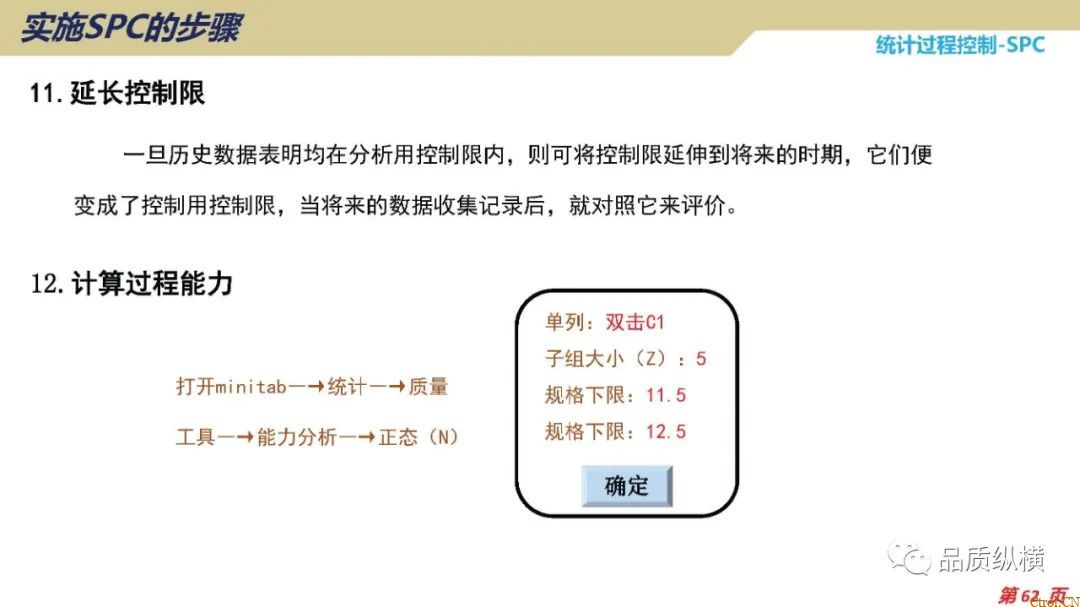
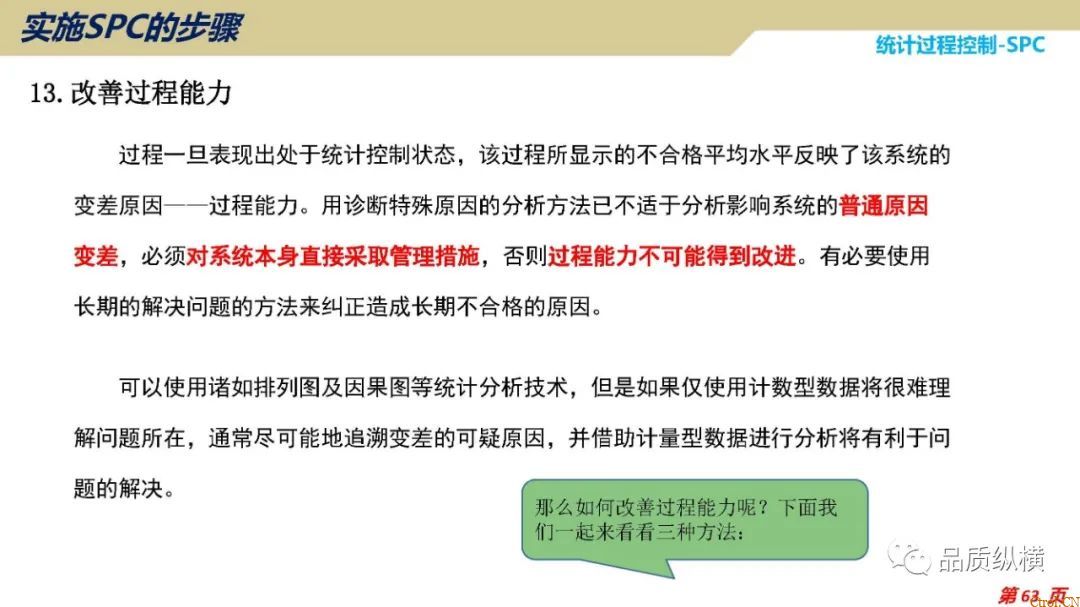
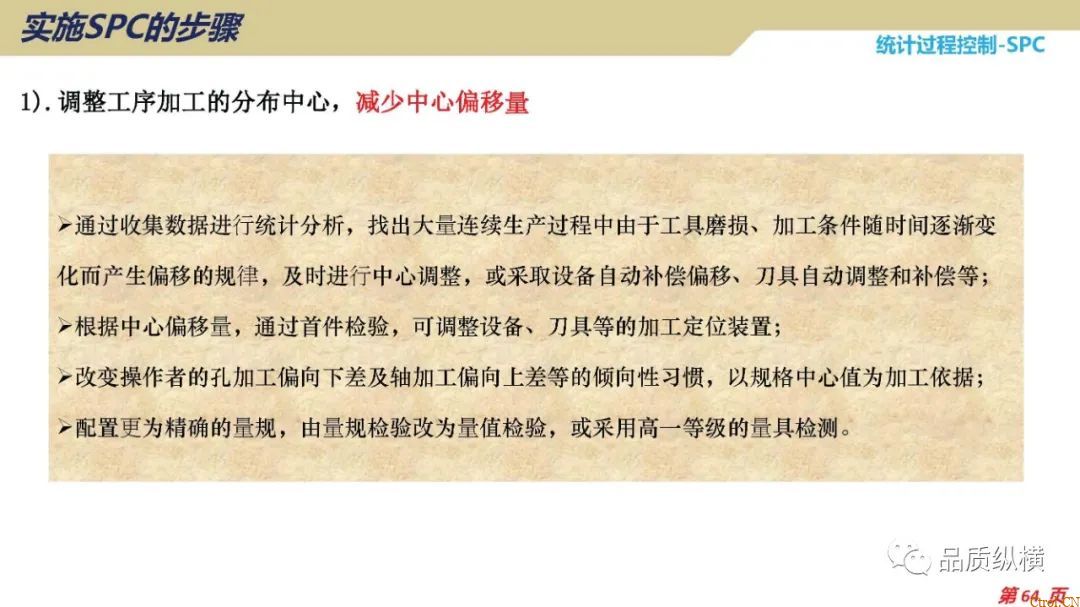
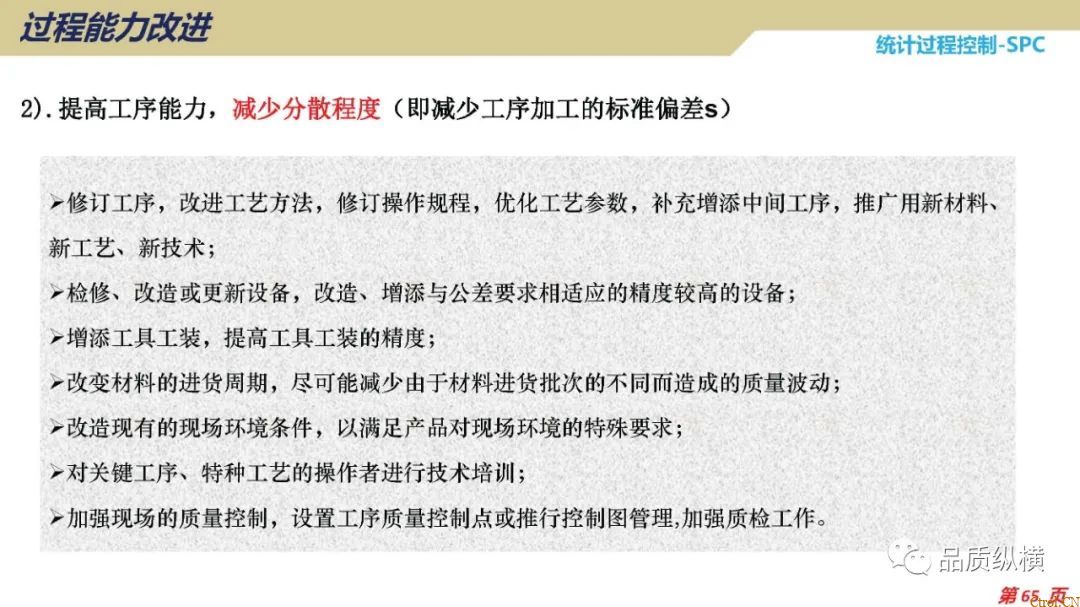
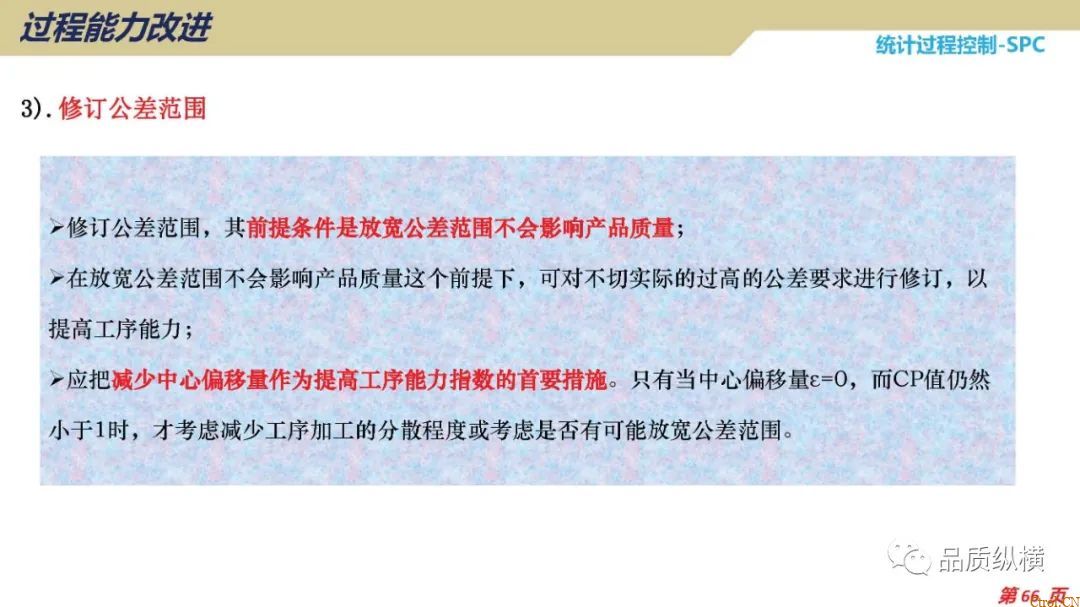
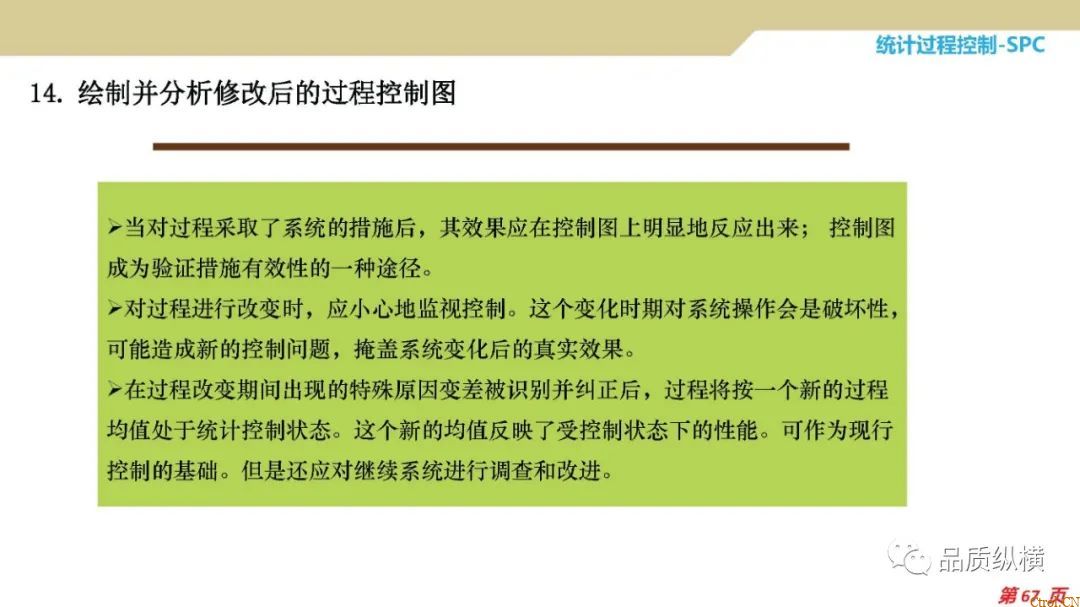
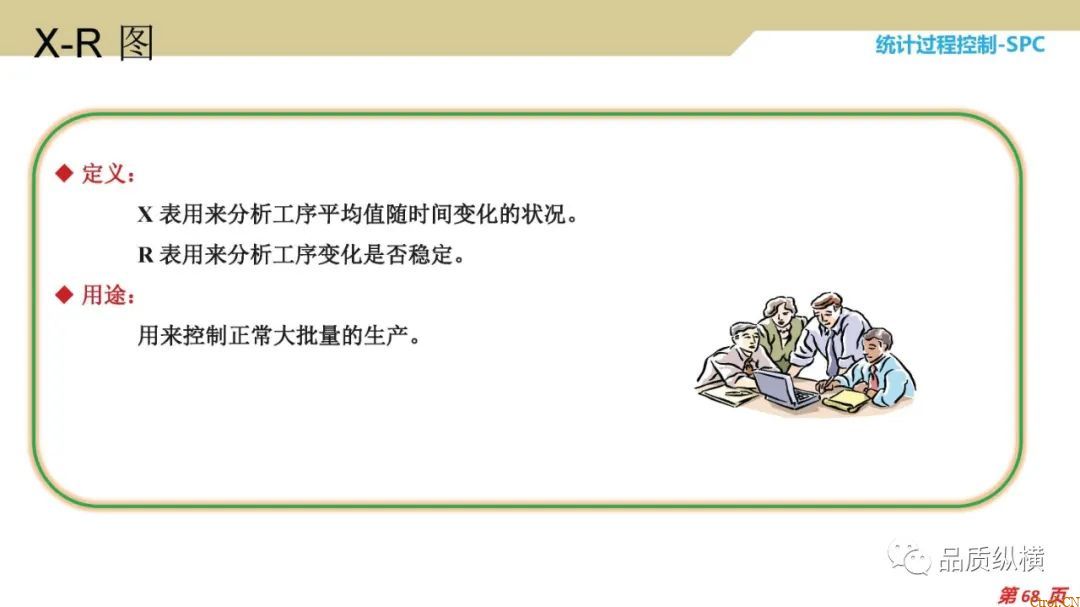
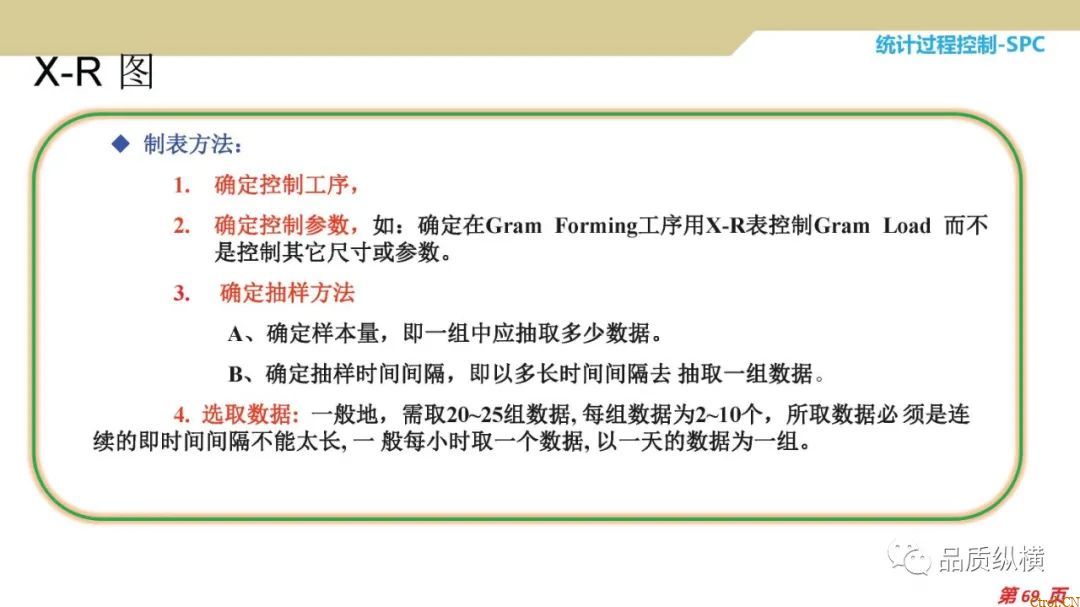
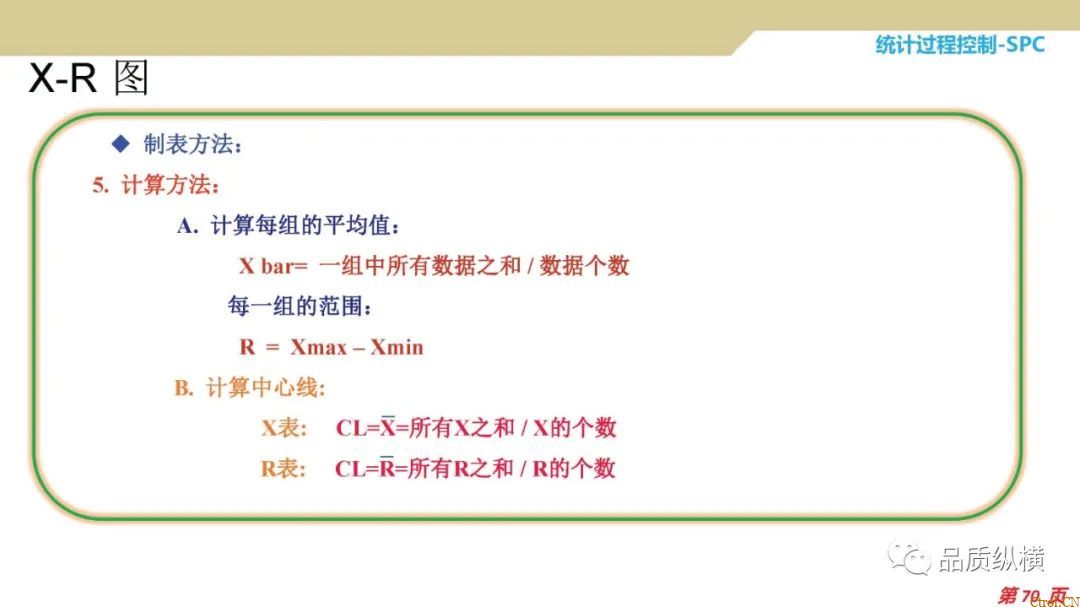
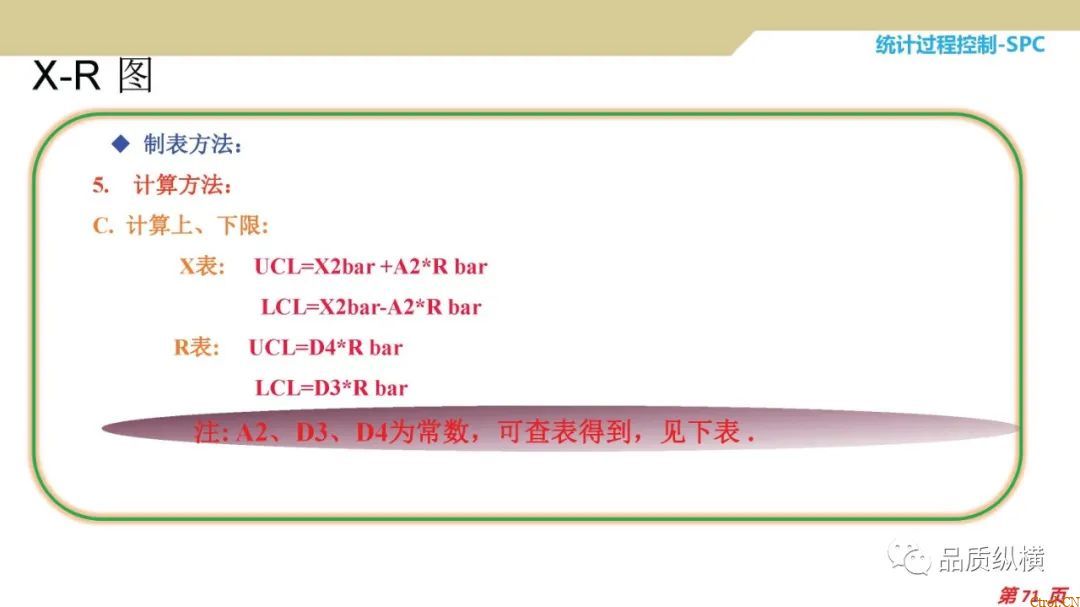
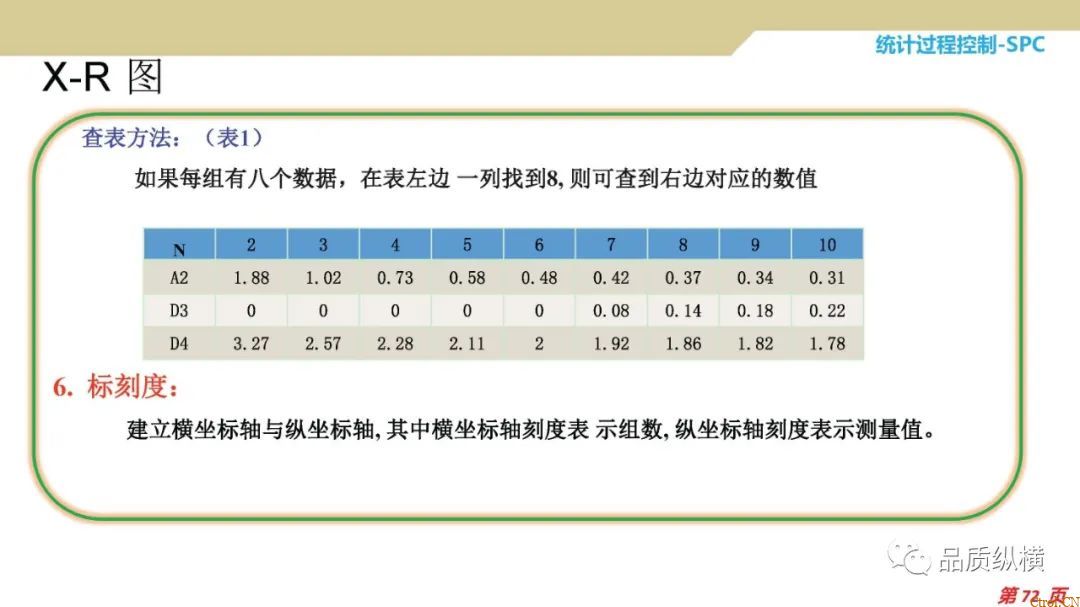
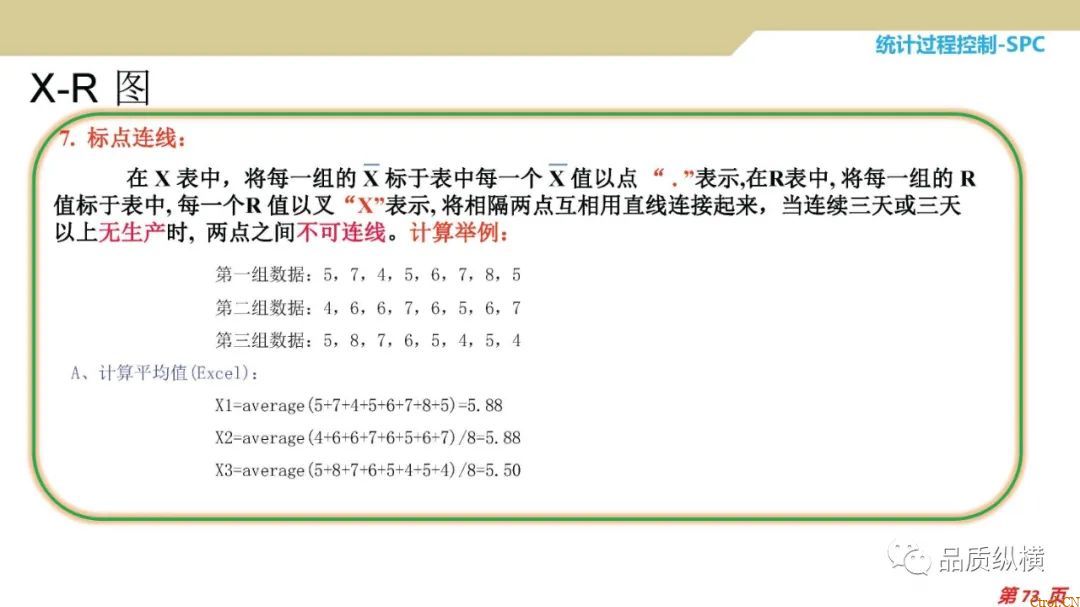
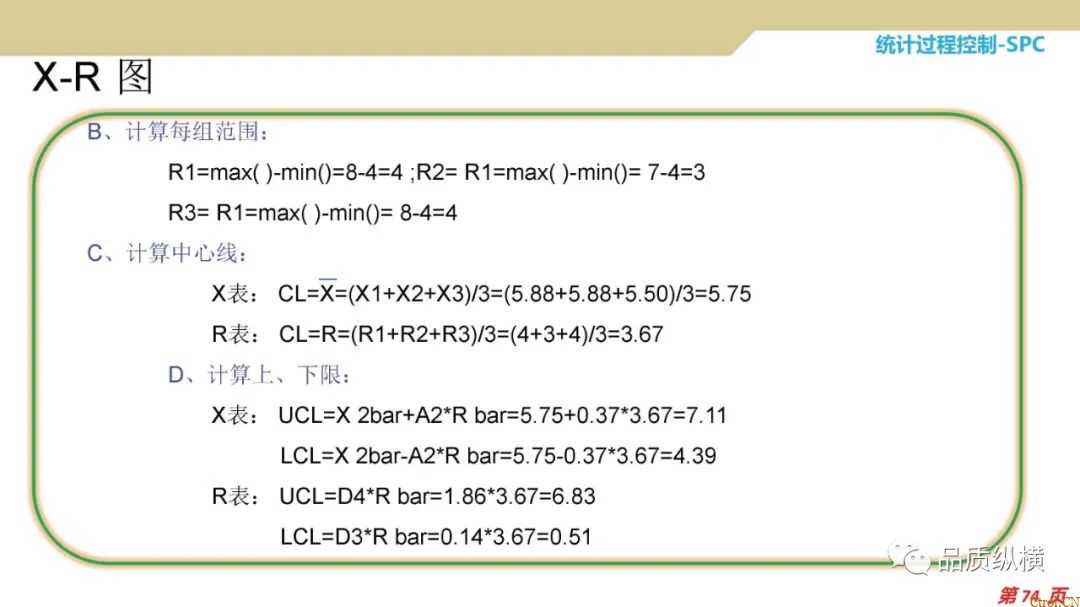
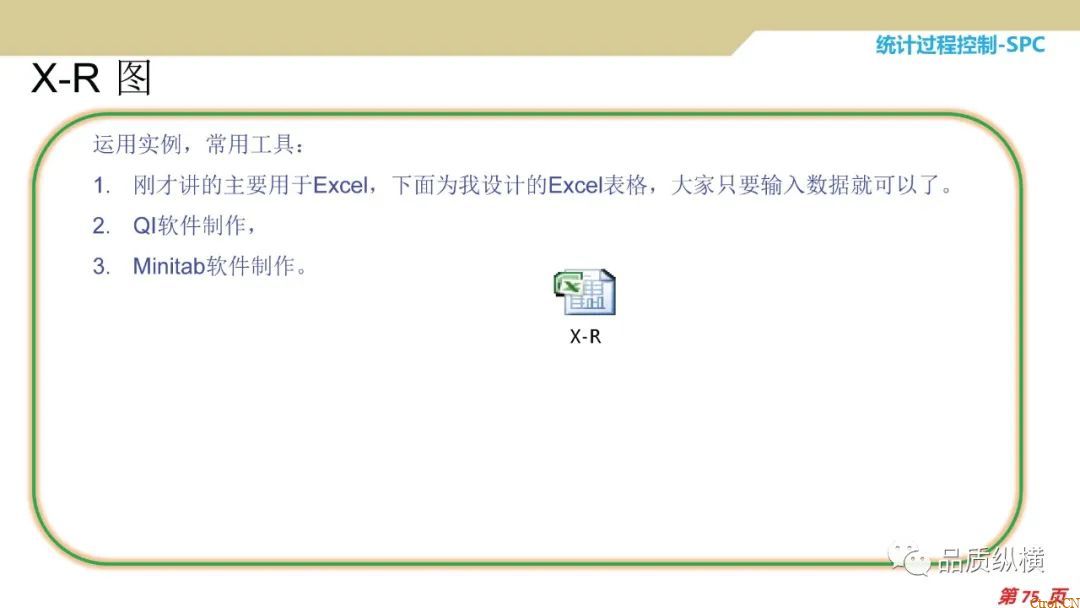
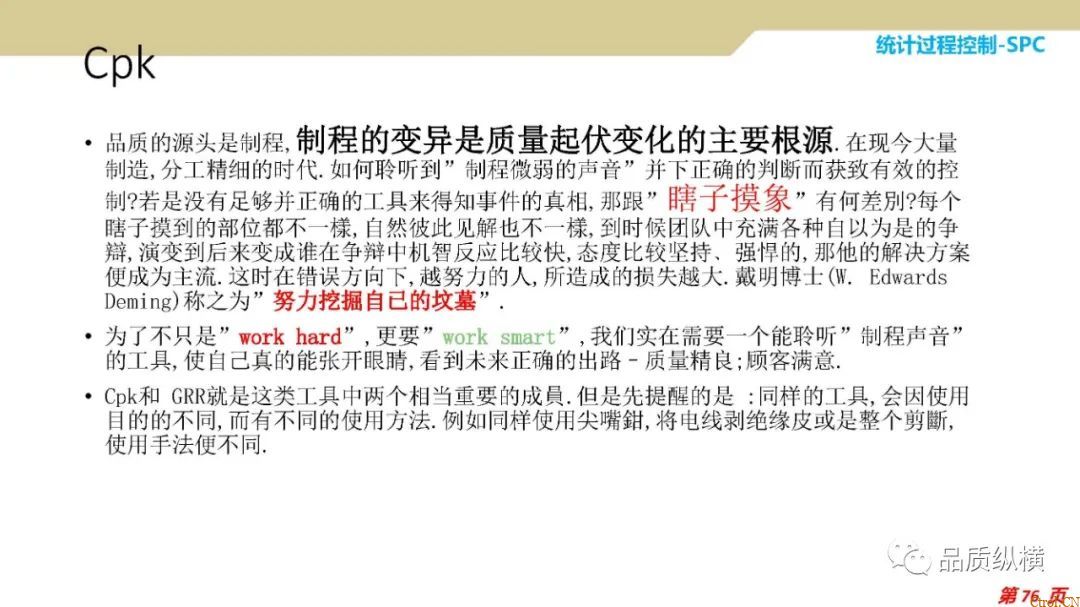
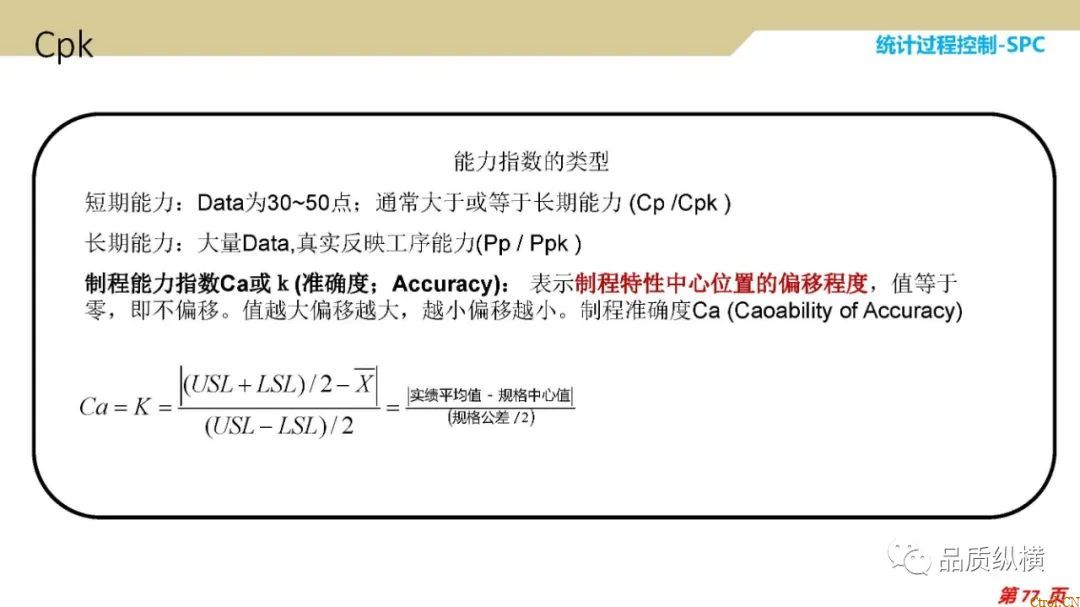
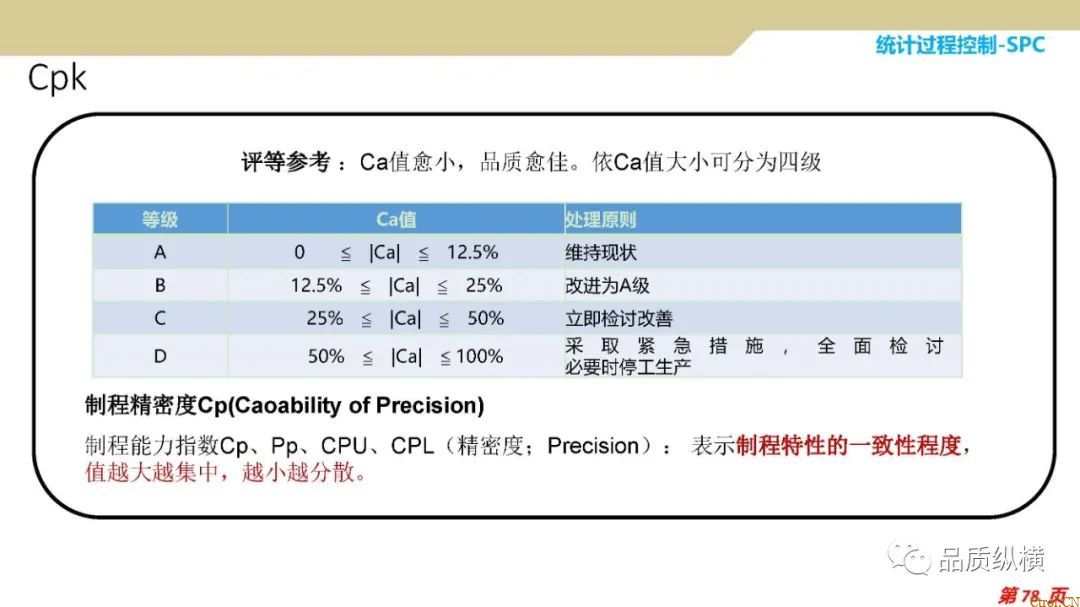
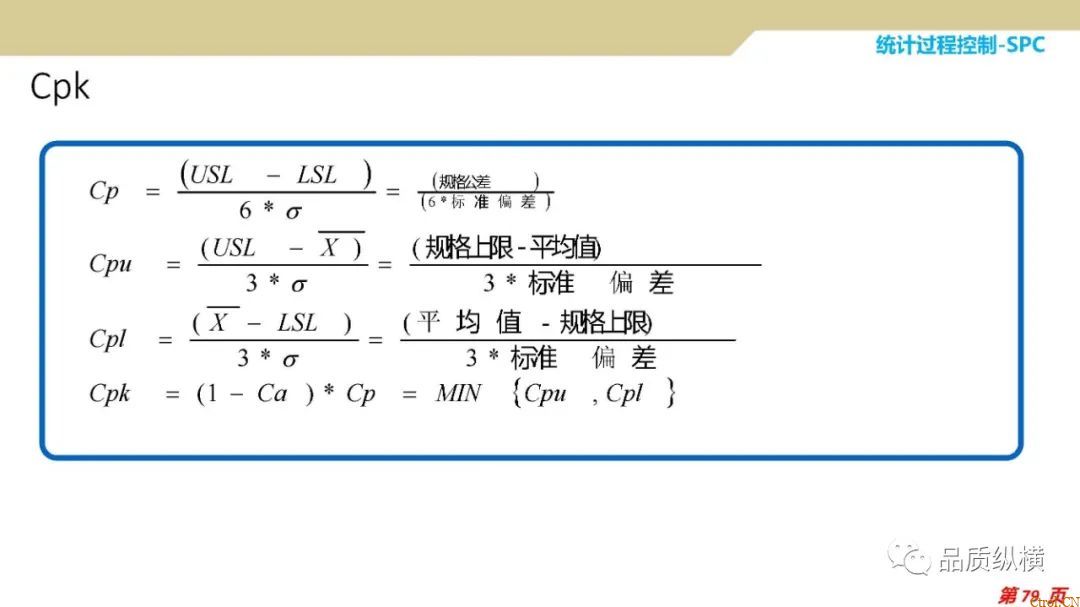
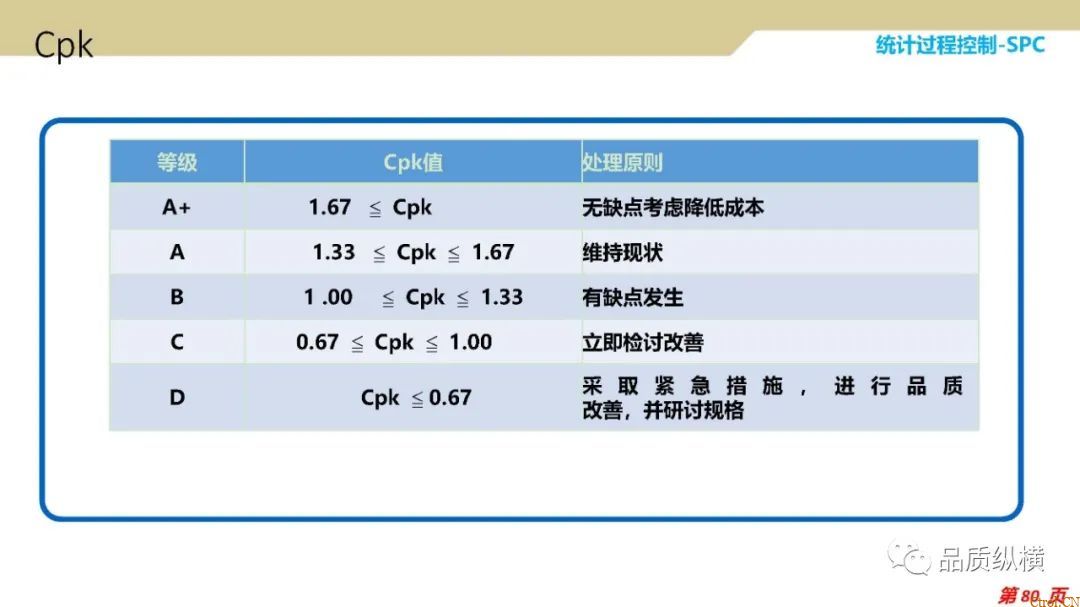
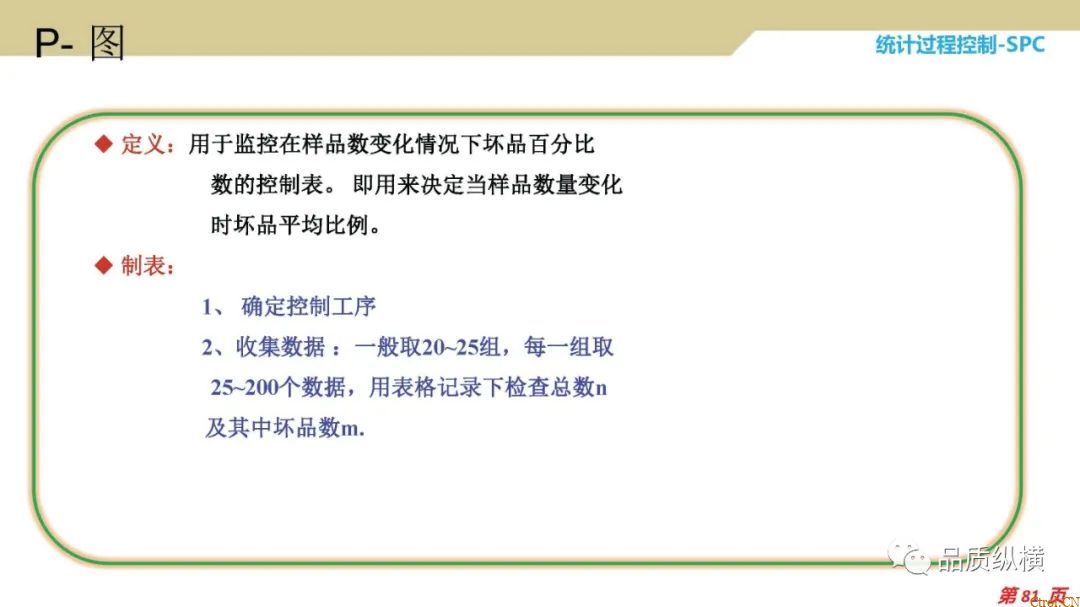
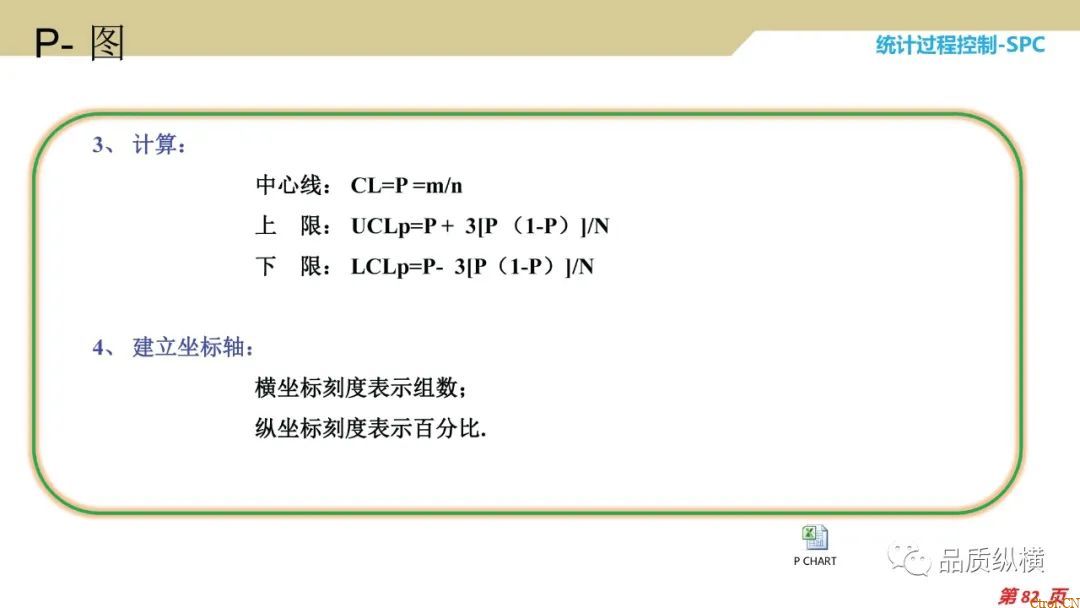
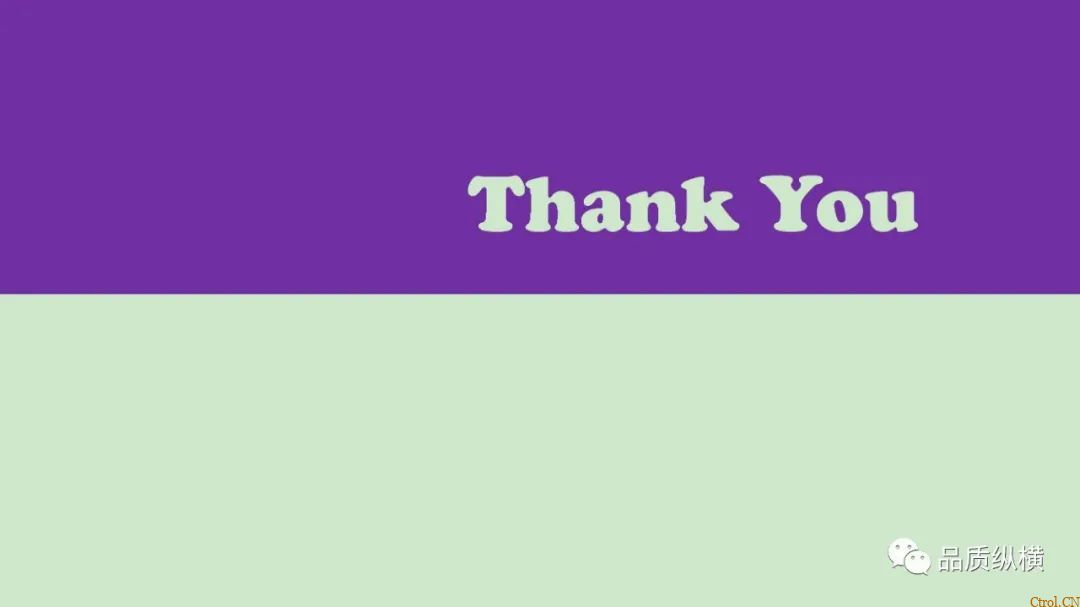