共计 2524 个字符,预计需要花费 7 分钟才能阅读完成。
本文主要用SEM和EDS对晶须、端盖金属和焊料材料进行表征。
近年来,由于传统Pb-Sn焊料会带来健康和环境安全问题,因此人们非常重视开发用于电子设备的电子互连材料的无铅(Pb)锡(Sn)基焊料。
使用无铅锡焊料的一个缺点是会形成锡须,这在1940年代首次报道。自1990年以来,电子行业已经报道了与晶须相关的失效故障,导致数百万美元的损失,主要是由于不需要的电桥而导致的短路和电流泄漏。
据报道,锡须在地球和太空产品的应用中都曾经导致了系统故障。迄今为止,有报道称至少有3次锡须诱导的短路导致在轨商业卫星完全失效。
锡须是一种导电锡晶体,从锡加工表面(在z轴上)自发生长,通常呈针状,直径通常为1至3 μm。晶须在没有施加电场或水分的情况下会自发生长,并且不受大气压力的影响。
锡须生长的机制已经研究了很多年。对于这种生长机制,目前还没有建立被广泛接受的解释,但业内对于锡须的形成已经达成了共识。
锡须的生长主要归因于镀锡中的应力。这些应力可能来自许多来源,包括:
1 电镀过程中产生的锡残余应力;
2 金属间化合物(IMC)的形成,尤其是在锡晶界内;
3 压应力,例如由螺母或螺钉的扭矩引入的应力;
4 电镀后表面弯曲或拉伸;
5 电镀材料和基板之间的热膨胀系数 (CTE) 不匹配。
在钻孔工具的产品测试期间,该产品电子设备的印刷电路板(PCB)出现故障。电路板在180°C下经过120小时的老化循环,然后在-40°C和180°C之间进行10 次热震循环(每个循环为2小时),然后发现故障。在检查过程中,在无铅焊料(Sn96)表面观察到许多白须。此外,观察到PCB安装芯片的引线键合断裂,这导致了电路板的故障。
本文讨论了锡须形成的可能原因。
首先,在体视显微镜下以各种放大倍率(10到40倍)对电路板进行宏观检查。在SEM下检查晶须和焊点的形态细节。据观察,PCB上过度涂覆了SCC3涂层,涂层呈棕色,这表明涂层在测试温度下发生了热降解。。在组件的所有焊点上观察到锡须。所有的晶须都是针状的,从焊料表面的涂层上脱落。
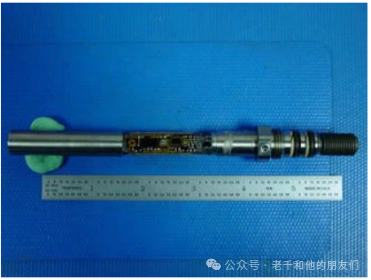
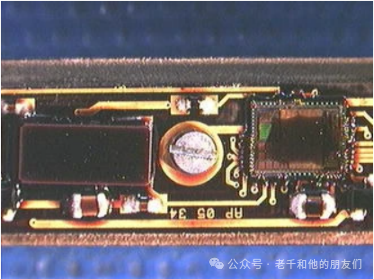
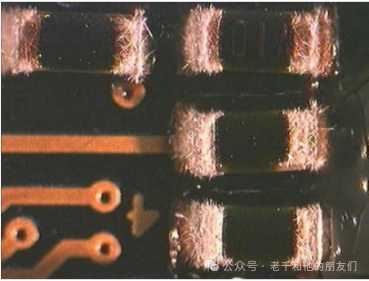
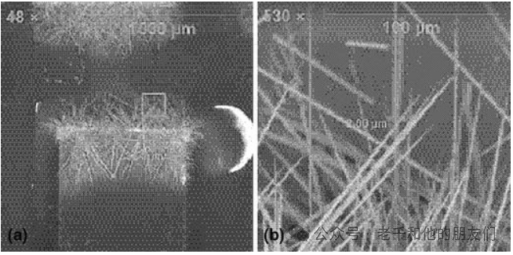
为了表征晶须的组成和在焊料基体中生长的可能的金属间化合物(IMC),使用EDS在SEM下对焊点进行横截面检测。
SEM/EDS对晶须和焊料材料进行检查,确认焊料为Sn96,晶须为纯锡。在140 小时的热循环测试中,晶须长出344 μm,晶须的宽度确定为2 μm。
电容器端盖横截面的材料表征确定了镀层中镍、铜和金元素含量。这表明:(a)端盖的镍层镀金,以及(b)端盖金属化的大量镍和铜已经扩散到锡层中。
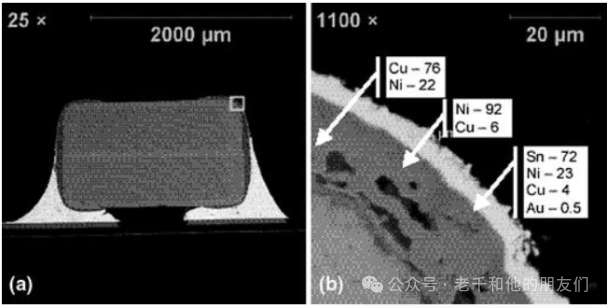
电容器焊接区域的横截面(其中长出了许多晶须)在端盖/焊料界面处识别出Sn-Ni-Cu和Sn-Ni-Au IMC层。在 IMC/焊接界面处观察到 Kirkendall 空洞链。在整个焊料基体中也发现了Sn-Ni-Au IMC 的岛。
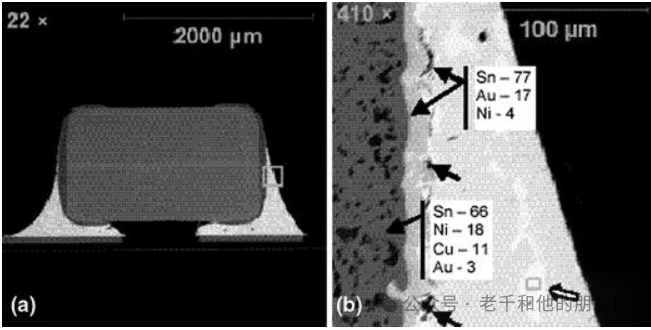
对PCB组件的工艺调查确定,涂有镍和金的铜基板与Sn96焊料(96.5Sn/3.5Ag) 连接。最外层的镀金铜衬底用于保护衬底免受腐蚀和氧化,镀镍层提供扩散屏障,抑制铜锡金属间化合物的有害生长。
然而,在锡基焊料和Cu/Ni/Au金属化的这种组合中,温度是避免界面反应需要考虑的关键参数。在测试温度(175 °C)下,锡基焊料和Au/Ni/Cu 金属化之间似乎确实发生了界面反应,这导致在焊料基体中形成Sn-Au-Ni金属间化合物(例如 Sn4AuNi2)。
人们普遍认为,锡焊料中的压应力是形成锡须的关键因素。锡焊料中的压应力可能是由(a)IMC生长,(b)热诱导应力(如热循环)或(c)机械诱导应力引起的。在这种情况下,端盖金属化扩散到焊料中并形成金属间化合物似乎是形成锡须的关键因素之一。
锡焊料中相当大的压应力可能是由Sn-Ni-Au金属间化合物的大量生长引起的。端盖金属化从高能区域扩散到低能区域为晶须生长提供了原子质量传递。热循环也可能导致焊料基体中压应力的增加。机械引起的应力,作为晶须形成的原因不太可能,因为不可能在主体 PCB上施加机械应力。
这些发现与高温退火可能降低锡须生长风险的推测相矛盾。Zhang等人假设高温退火会影响锡和铜衬底之间IMC 的形成。这可能是因为目前尚未充分研究有关时间、温度、焊料类型、基材和阻挡金属层的因素,无法为应用退火来减少锡须形成提供足够的指导。这些发现还表明,正如文献中所声称的那样,保形涂层的应用可能不足以遏制涂层内的胡晶须生长。
结论和建议
Sn96焊点上锡须的形成归因于焊料材料中产生的压应力,这是由于端盖金属过度扩散到焊料基体中并形成 Sn-Ni-Au 金属间化合物。PCB 的热循环也可能会增加锡焊料基体中的压应力。
在端盖/焊料界面处鉴定出大量金。金含量高(高达17 wt.%)可能是由于组件端盖镀金过多。在使用温度下,端盖金属化扩散到焊料材料中,导致在整个焊料基体中形成Sn-Ni-Au金属间化合物,并在端盖金属间化合物/焊料界面处形成许多“Kirkendall”空洞。
锡须是直的(针状),很长(0.344mm),数量很多,它们可以从SCC3保形涂层中生长出来。这表明保形涂层无法控制锡须的形成。
端盖金属化似乎无法抵抗180 °C的测试温度。因此,建议在测试温度下充分研究端盖金属化与焊料材料的相互作用,以避免在焊料基体中形成金属间化合物。
在PCB的高温测试中,需要仔细考虑镀金层的厚度、元件基板的性质以及接头中的焊料量。厚度为0.05至0.2 μm 的沉金层足以提供可焊性保护。如果金层太厚,最好在焊接前将其变薄。这可以通过热焊料浸渍程序来完成,其中熔融的焊料用于洗去金层,用一层焊料或锡代替它。